助力智能制造——精益生产现场管理与可视化
企业简介
日丰企业集团有限公司是中国新型塑料管道研发生产与推广应用的知名企业,是中国塑料加工工业协会塑料管道专业委员会副理事长单位,国家火炬计划重点高新技术企业,同时也是管道与卫浴全面发展的大型建材产业集团。
自公司成立以来,日丰一直将产品品质视为企业发展壮大的核心竞争力,坚持走品质为先的发展道路。日丰公司拥有国家认定企业技术中心、CNAS认证实验室等研发机构,获得800余项国内外专利,这些都为产品品质提供了的坚实保障。在涉及产品的原料选购、生产运输等环节,日丰公司严格加强把控,每一个工序,每一个细节,都做到精益求精。
日丰产品还通过美国NSF、德国SKZ等50多项国际认证,畅销全球的100多个国家和地区,荣获全球亿万用户一致认可与广泛赞誉。
一、业务/管理需求/挑战
1、在市场快速变化的后疫情时代,通过精细化管理实现降本增效变得尤为重要。以往生产看板主要体现综合运营情况,没有对问题做细分与挖掘,已经不适应当前的经营管理目标。
2、数据标准化程度低。近几年业务快速增长,增购产线、管理架构调整的情况增多。因为忽略了对系统基础信息的同步更新与维护,所以数据缺失、值异常情况明显越来越严重,实用性不高。
3、数据自动化程度低。由于生产数据不完善,日常统计分析仍需依赖车间人员以传统的系统导数+人工合并处理的方式进行。 每日上班后需要在1小时内对前一天的数据进行下载合并、关联计算、更新替换,时间紧急且容易出错。
4、管理流程缺乏闭环。由于信息离散,维度不统一, excel分析方式不能直观地发现各个指标的关联关系,缺少便捷的全盘布局方法。信息可视化与管理工具脱节,难以追踪问题解决进度与改善的效果。
二、解决方案
以减轻车间日常数据处理工作为切入点,重新对生产管理做全流程梳理,目的是信息全面化,数据可视化,对制造过程的问题及时预警。
1. 蓝图设计:现场调研车间管理现状与未来规划,提取生产计划、物料利用、人员管理、设备效率等内容,设计出看板的蓝图。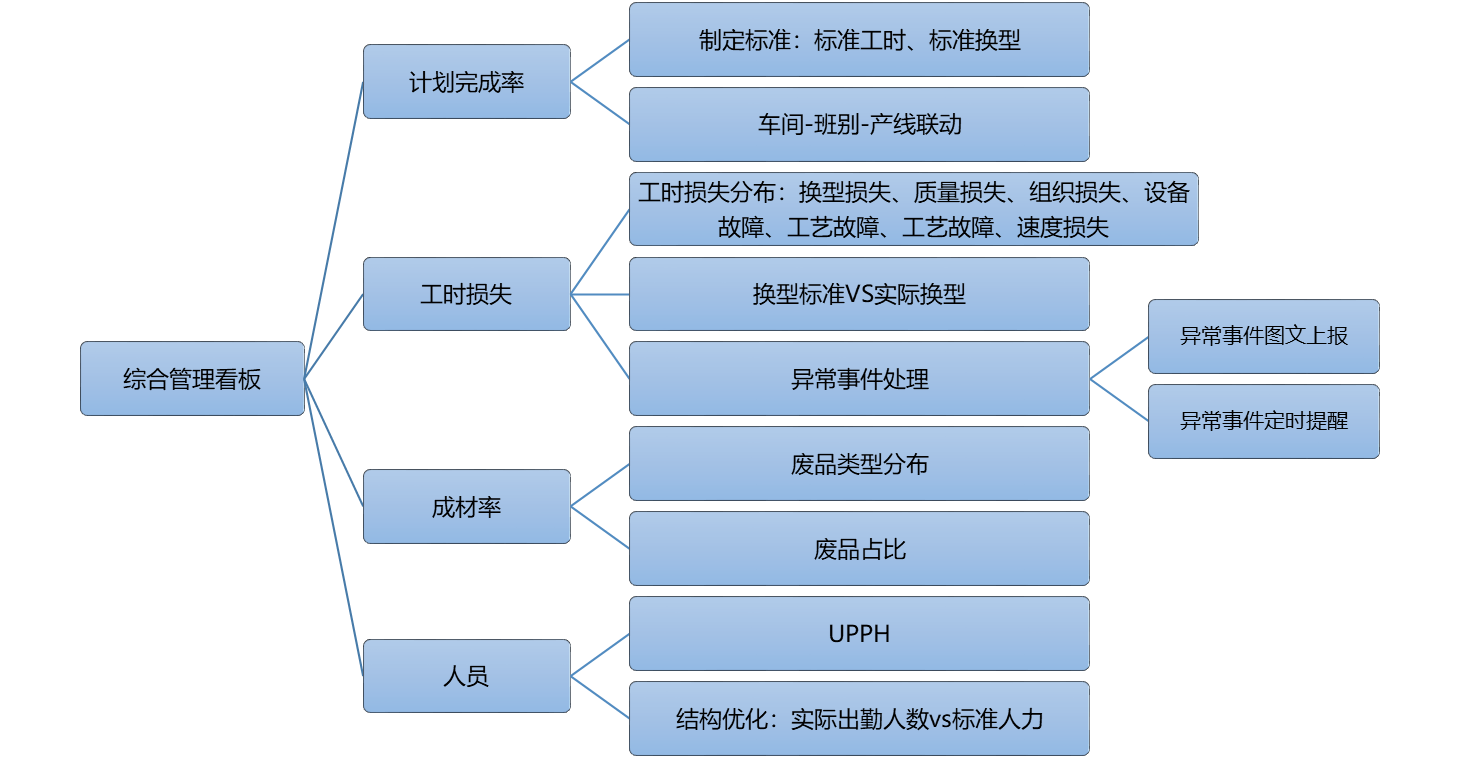
2. 内容制作:一切业务数据化。结合填报功能,通过大数据平台整合各个生产数据库的数据,解决了数据孤岛问题。
通过联动,下钻,参数的设置实现多维度分析,搭建起生产可视化看板。同步进行管理标准化,包含前端数据录入规范,基础信息及时维护,确保报表准确性。
3. 优化迭代:精细化管理各项生产指标,定义标准换型工时与产出,标准人力,更新标准工时,系统新功能上线。图表查看、填报维护及异常事件上报设置统一入口,避免分散管理。
三、业务/管理应用场景
3.1 场景一:搭建现场管理实时看板
痛点:缺乏现场管理的相关报表,信息传递滞后。生产计划控制人员主要通过需要系统导出数据,走现场,或产线负责人主动告知的情况下了解生产状况,然后调整生产计划,且在工作繁忙的时段,难以兼顾各个车间的产线。
解决方式:按照目视化颜色管理的原则,对关键指标分别设置标准范围,直观发现异常数据,便于定位问题。设置班别、品项、产线的参数,按照品项-班别-产线-每小时的维度逐步进行计划完成率细化。对于某时段未达标的产线,通过产线生产状态预判是否出现计划外的异常问题。除了表现当前生产状态,同时进行横向与纵向对比,不同产线对比,同产线的不同日期对比,提供多维度分析方法。
场景价值:以前只能通过系统导出数据并整理计算的方法了解当前生产,现在能实现远程监控+现场沟通的方式,生产计划的跟踪和调整更加方便灵活高效。
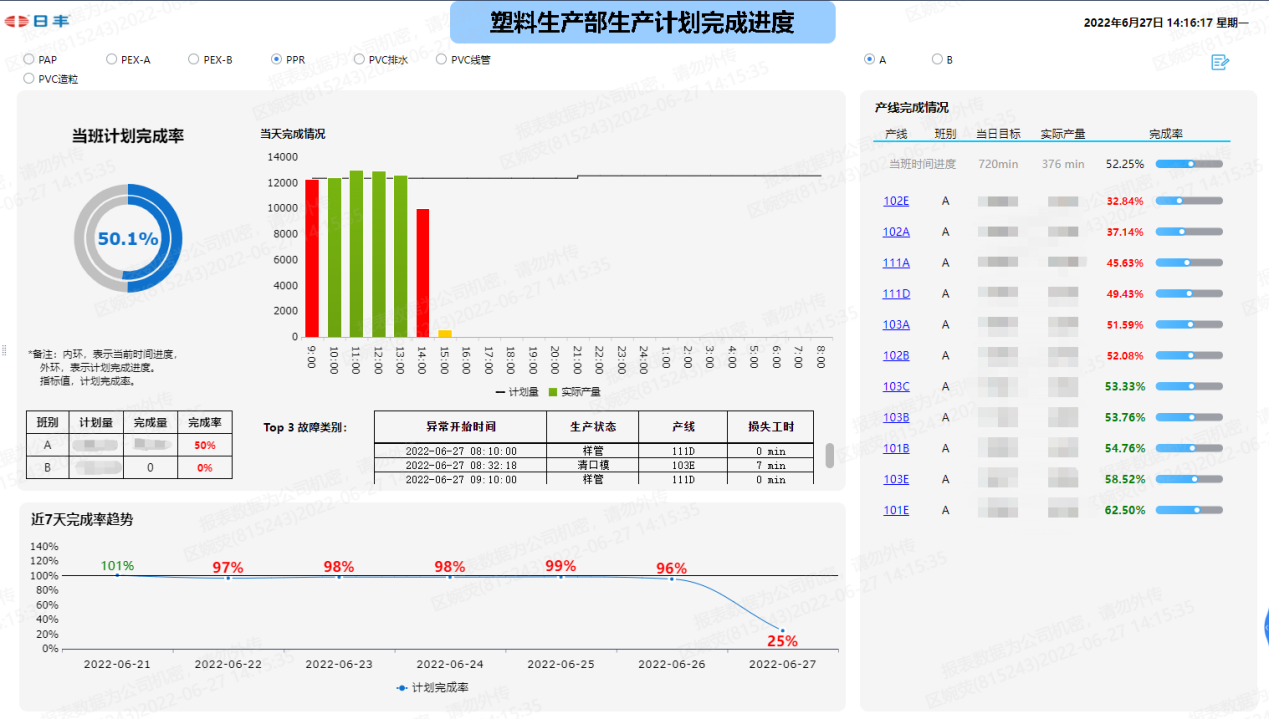 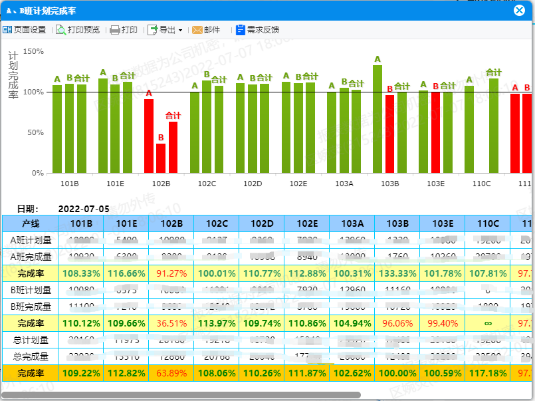
3.2 场景二:搭建生产综合运营看板
痛点:目前每日会议准备时间长,下载数据、处理数据耗时长。受限于Excel处理过程的复杂繁琐,效率、成本等方面的分析还未实现。工厂的生产信息化、透明化程度低,缺乏全局统筹的管理模式。
解决方式:明确管理的目标,搭建以提高产量达成为核心,以降低损耗、提高设备综合利用率、提高人均效能的综合运营看板。
设置工时损失超链接,各填报报表超链接,统一页面查看与维护各生产流程的信息,提高信息获取的便捷性。
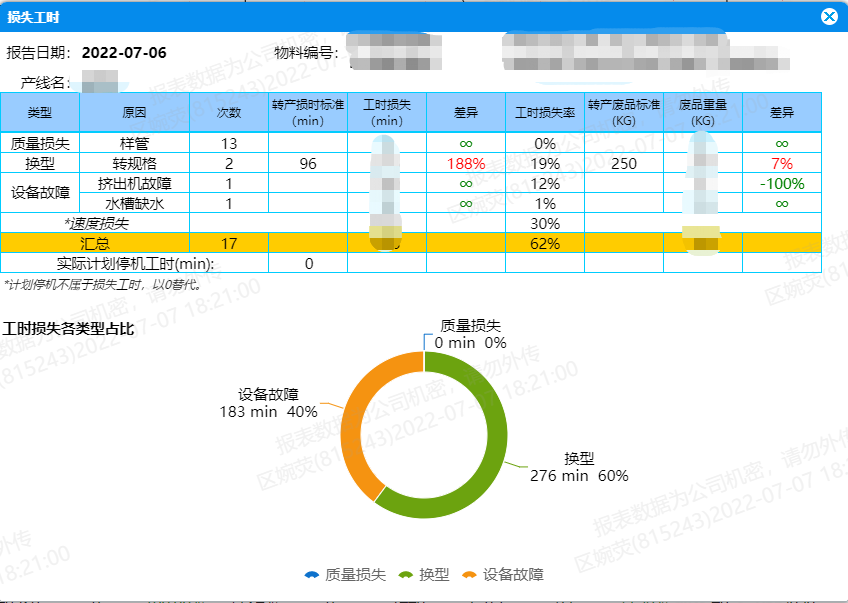 场景价值:统一了数据输出口径,节省75%的人工处理的时间,完成生产各模块的内容分析。
3.2 场景三:生产异常上报与提醒
痛点:各个车间负责人通过excel记录每次发生的异常事件,在每日早会进行问题上报,提供解决方案。信息收集的方法导致信息会有延迟,管理者希望能更快发现问题并了解问题处理进度。再者,如何降低常发性问题,并尽可能做到提前准备,成为管理者迫切想解决的问题。
解决方法:由于以往的登记信息不够结构化,不利于后期进行信息提取和数据分析,按照5W2H分析法重新设计填报模板,增加图片上传的功能,便于图文并茂阐述问题,能更直观的了解现场状况。通过定时调度的提醒功能,发送新增的异常事件给相关负责人,有新增异常问题则进行推送,否则不发送通知。
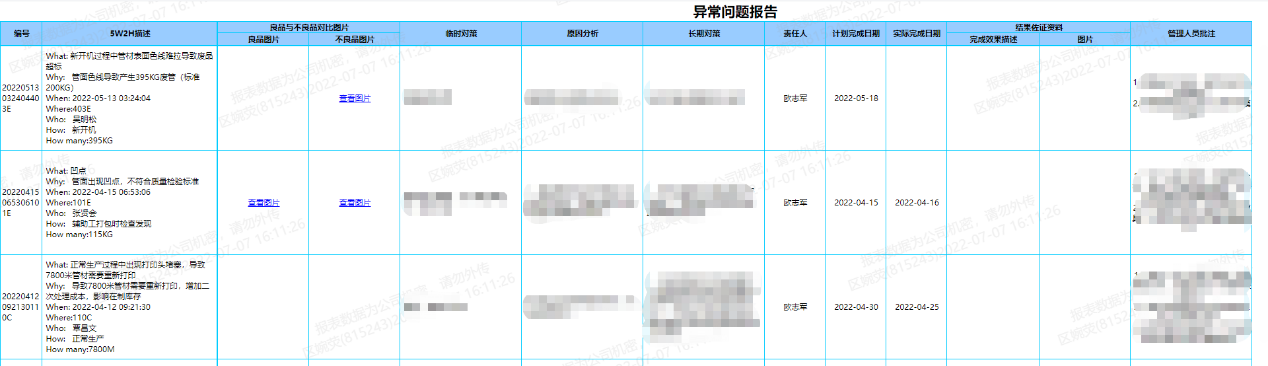 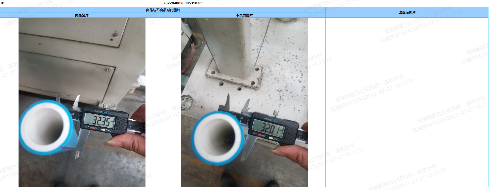
场景价值:线下管理转化为线上统一管理,通过定时推送,管理者及时了解现场信息反馈,为下一阶段的设备数据挖掘与问题预警做数据基础。
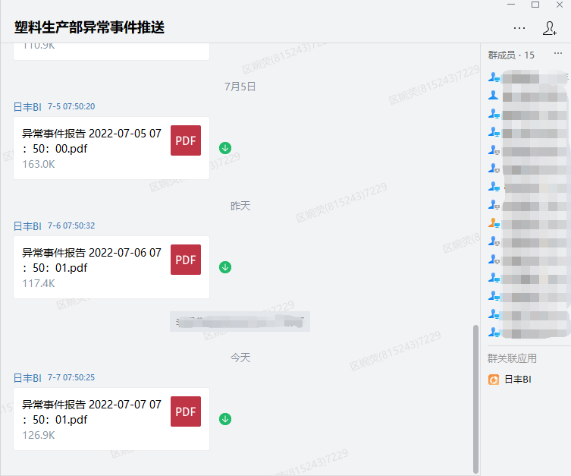 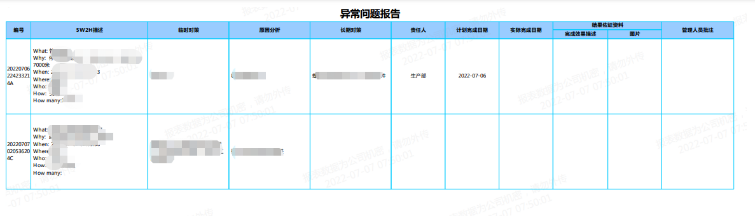
四、总结与展望
- 生产看板节省了数据处理时间,统一了计算口径,同时通过BI的功能充分把各种管理需求进行整合。管理者能随时了解生产现状,专注于提高设备生产效率、提高产量等方面。
- 在梳理业务流程的过程中,车间意识到数据标准化的必要性,以往没有做好的细节重新重视起来,因此制定了标准维护方法,并安排定期回顾与修改。只有不断培养企业人员的数据思维和精益管理思想,才能巩固和扩大在改善过程中的获得的成果。
- 信息化与自动化为大数据分析与智能决策做基础。日丰非常重视数据自动化采集与端到端业务的链接,已具备完善的管理系统并积累了丰富的数据。通过此次生产数据赋能的项目,打造了信息透明、管理可视化的工厂模式。下一阶段,日丰将会横向拓展至其他生产基地,纵向关联上下游业务,提高跨部门协同效率,降低内部沟通成本。
|