聚焦业务视角,实现数据共享、智能驱动系统
企业简介
苏家屯车辆段是中国铁路沈阳局集团有限公司下属最大的铁路货车检修单位,位于苏家屯铁路枢纽,下设10个科室和22个车间,年均货车厂段修能力26000辆、临修车能力40000余辆,轮轴检修能力85000余条,轮轴生产能力15000余条。我们单位的主要任务就是服务铁路货物运输,为铁路货物运输提供优质车辆。我们服务的主要企业有鞍钢、本钢、华晨宝马、北良集团、辽化、大连港、营口港、丹东港以及各个热电厂等。
业务管理需求\挑战
苏家屯车辆段原来在轮轴生产及检修相关业务方面仅有一套HMIS系统,用来采集轮轴轮轴检修及生产加工过程中的技术数据。这些技术数据也仅是用来生成轮轴卡片,证明检修质量合格。而轮轴生产及检修实际上是一个覆盖生产、调度、材料、核算、技术、质量等多个业务范围的系统化过程。我段原有的系统建设与实际需求出现了巨大差距,而这一反差也给我们的工作造成了很多问题,其中比较突出的有:
1.数据采集方式落后,采集成本高、人力资源浪费严重,数据准确性低
原来使用的数据采集方式是人工填写或打印纸质记录,随工件在工艺线上移动,最后再由专职录入人员集中录入HMIS系统。这种方式存在低效采集和重复采集问题,直接造成了人力资源的需求增加和浪费,同时还制造了较多的错误数据。
2.数据的信息化、数字化应用渠道单一,与实际业务需求差距大
我们采集的轮轴检修和生产加工数据,HMIS系统只能用于生成两种《轮轴卡片》。而我们的《轮轴检修规程》内规定的需要我们生成标准记录有47种,其余的45中均需要人工统计分析来完成。其他的调度、材料、财务等数据的统计分析也都需要人工完成。有些统计分析通过人工是无法实现的,这也造成了我们无法全面掌握轮轴生产的真实情况。
3.生产、调度、质量、材料、财务等部门间存在壁垒,数据交互慢、交流量小
以生产数据为例,每日生产部门只能通过excel方式向调度汇报整车检修数量,对于轮轴检修数据没有相关统计上报。而材料、财务部门就更无法掌握当时实际消耗材料和生产直接费的核算情况。
4.无法有效生成准确的生产经营数据。最为典型的问题有:工作者不知道自己当天的准确工作量;管理者只知道当日的大的任务数,实际生产细节不掌握;阶段性统计统计需要反复进行,且每次都存在偏差。
面对以上问题,我们急需建立一套合理设置数据采集方式,打通数据壁垒,实现数据自动归集运算,进行可视化的数据展示的系统。为了实现建设这一系统的目标,2017年我们就开始对系统建设进行摸索,尝试过委外合作开发、引进成型系统、培养人才自主开发等方式,真可谓是“路漫漫其修远兮,吾将上下而求索”。在尝试过程中,遇到的较为突出的矛盾有需求与开发对接的沟通存在鸿沟,需求更改需要增加开发支出,成型系统与实际业务流程不符无法使用,自主开发人才培养困难效果差。
寻找就能寻见,经过三年多的探索,在2020年下半年我们从网上知道了帆软报表开发平台,经过进一步了解,我们确定这个平台完全能够实现我们无纸化流水线、线上业务流程、自动统计分析、可视化效果展示的开发需求。
三、解决方案
本项目基于对轮轴生产检修全过程进行信息化、数字化、智能化的管理需求,以轮轴生产检修工艺过程为主线,同时融入轮轴生产检修相关管理部门的业务流程,通过报表开发规范化、数据采集信息化、审批流程网络化的手段,实现流程控制智能化、统计分析自动化、主要数据可视化的目的。
1.报表开发规范化
为了报表数据、报表内容、报表风格、报表功能的一致性,我们进行了报表开发规范。按照数据层面、工程层面、报表层面、功能层面、UI层面进行分类,制定贯穿开发全过程开发规范。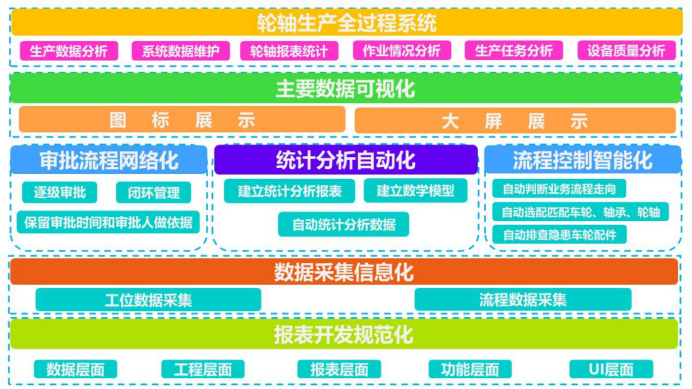
2.数据采集信息化。针对流水线和业务流程分别进行设计开发,实现数据采集分散至各数据生成的工位。流水线按照工艺流程内的工位设置以及标准采集项进行开发,业务流程按照流程环节进行开发。
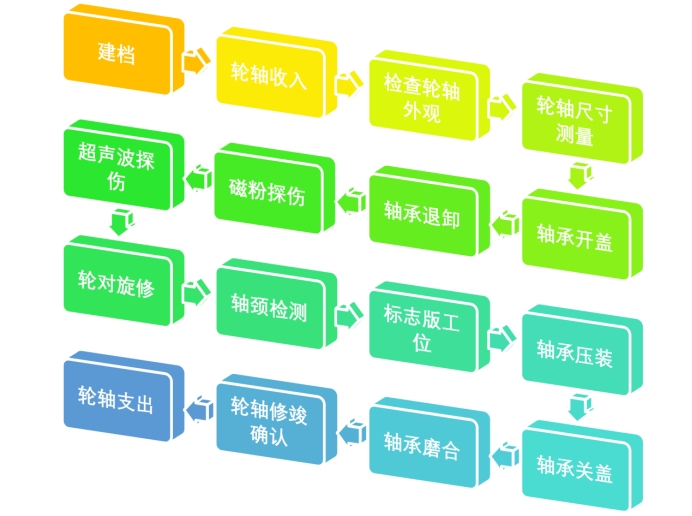
3.审批流程网络化
所有涉及审批流程的业务办理,按照实际审批流程,从申请发起开始,经过逐级审批,直到最后的办理结果的整个闭环管理,都在网上进行。所有的办理环节,均保留班办理人、实际办理时间等相关办理数据。
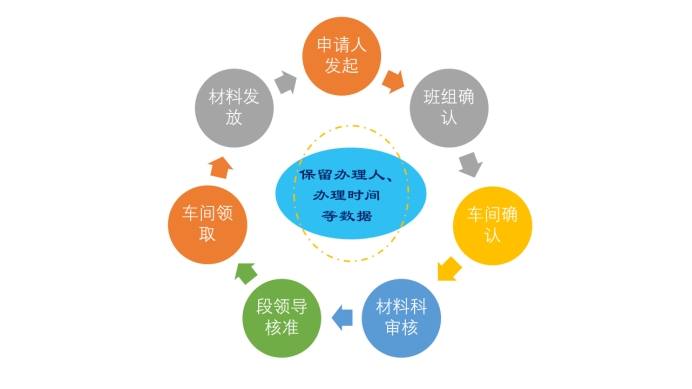
4.统计分析自动化
按照生产数据报表和业务流程报表的样式制作所有统计分析报表。按照报表内的计算项点、逻辑关系建立数学模型,通过调用数据库内容数据,实现所所有报表按阶段、部门、类型等分类的自动统计分析。
5.流程控制智能化
生产流水线根据工位的生产数据,自动判断应进行的工艺流程;业务办理流程根据数据自动判断业务流程走向;轮轴生产过程中根据车轴轮座直径自动选配匹配车轮,根据车轴轴颈直径自动选配匹配轴承;轮轴装车使用过程根据车轮直径,自动选配匹配轮轴;根据国铁集团发布的隐患配件标识,自动对轮轴装用隐患配件情况进行排查。
6.主要数据可视化
使用大屏对主要数据进行展示。
四、业务管理应用场景
场景一:无纸化流水线
痛点:
我们有3条轮轴生产线和1条轮轴检修线,共有90道工序138个工位需要进行采集数据。轮轴生产线每天生产50条轮轴,每条轮轴需要录入247项,268条数据。轮轴检修线每天检修约320条轮轴,每条轮轴需要录入227项,239条数据。原来我们采用打印标准卡片,工位人员填写本工位数据,卡片随着配件一起在流水线上流转,最后再由22名录入人员集中录入到系统。这种方式存在重复采集、采集效率低、错误率高的问题。
解决过程:
我们为这些工位公开发了103张填报报表,其中移动端31张,PC端72张。采集方式有手工录入和数据库接入两种。对于自动测量、超声波探伤、标志板打印、磨合等有设备生成数据的工位,我们都是使用工位机直接调取设备数据库数据。其他工位使用手工进行录入。手工录入操作报表的录入界面上,对于有固定的选项的填写内容,全部建立的数据字典,用了单选或者复选控件。同时使用系统生产条形码,手持机录入工位扫描条码即可识别配件身份。每个录入控件都设置了填入值自动判断,对于不符合技术条件的数值禁止提交并进行不合格数据提示。还将上道工序的生产数据携带至下道工序,下道工序工作者对前道工序采集数据进行复核。
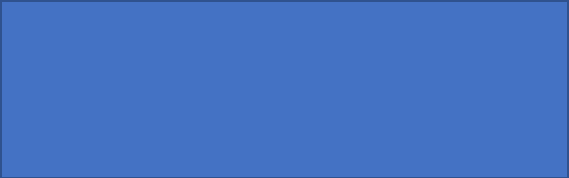 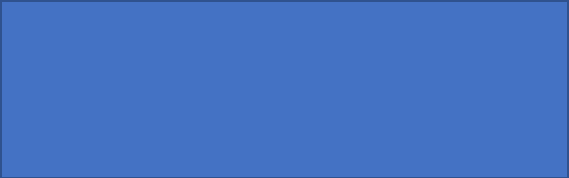 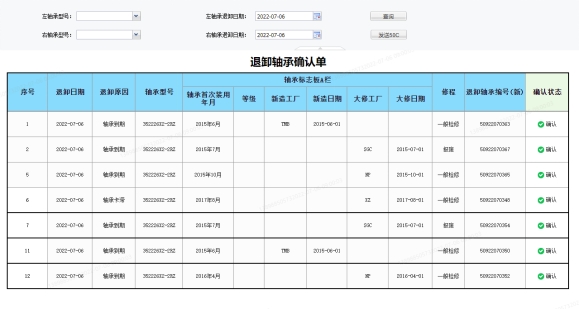 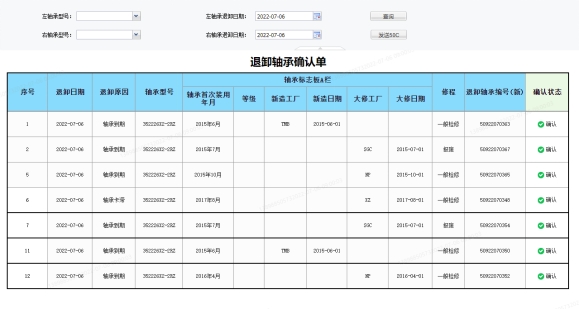
配件拆修工位退卸轴承确认单
 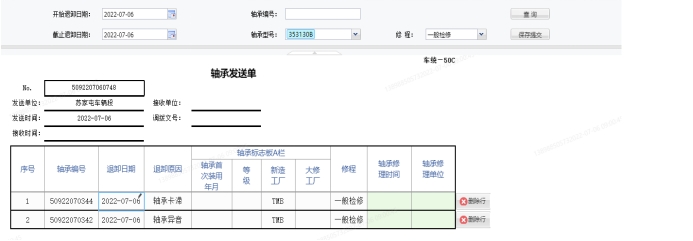
轴承发送工位轴承发送单
价值:
通过工位数据采集的实施,实现了无纸化生产现场。减少了22名录入人员,最终数据的准确率达到了百分之百。在有效缓解了近年来生产人员逐年较少的问题的同时,每年直接节省工资及附加费支出近330万元。
场景二:审批流程网上办理
痛点:
原有的线下审批流程在办理过程中存在较为严重的办理周期长,办理结果与审批流程未形成闭环,对办理流程过程进行追溯较为困难。
解决过程:
分别按照具体办理流程,开发了合同管理、物料请领、车轮车轴报废审批、轮轴发送、设备报修5个五个模块。
1.轮轴销售以及配件采购合同的网上审批和执行情况确认。所有合同在签订前需要进行网上预审,由承办人发起,部门负责人审核,法律顾问对条款进行审核,最后有领导审批完成后签订纸质合同。承办人、财务部门、法律顾问根据后续执行情况分别对开具发票、收支资金以及合同办理情况进行相关维护。
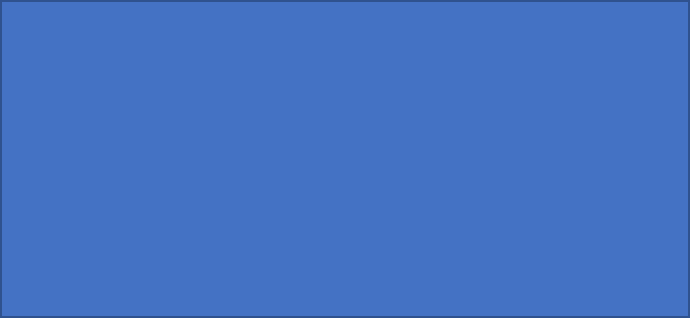 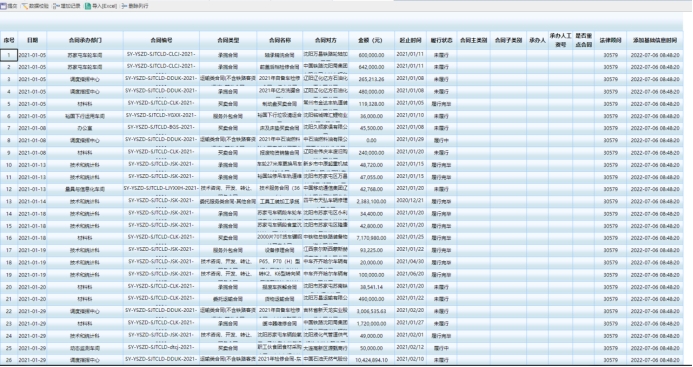
合同基础信息数据维护
2.物料请领网上办理
由生产班组发起申请,材料员进行审核,过审后数据流转至管库远处,管库员根据申请信息提前准备。生成电子版物料领取凭证后可进行批量打印。班组使用物料领取凭证到库房领取物料。
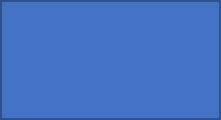 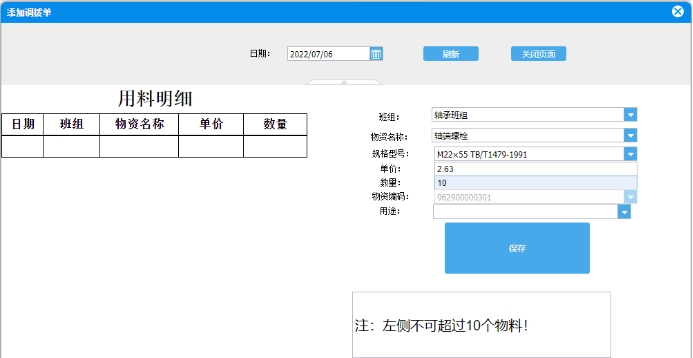
班组用料填写物料调拨单
3.车轮车轴报废审批网上办理
调取生产流水线生成的车轮、车轴报废信息,自动生成报废申请统计表和明细表。核实数据准确后,提交报废申请。相关业务部门按照流程进行最终核实审批。
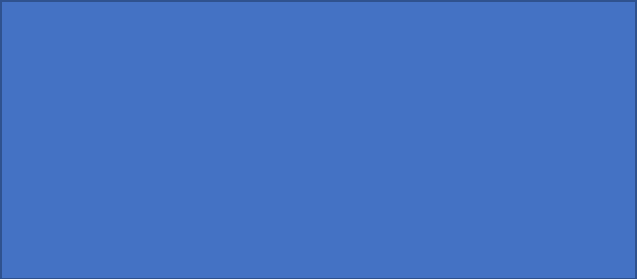 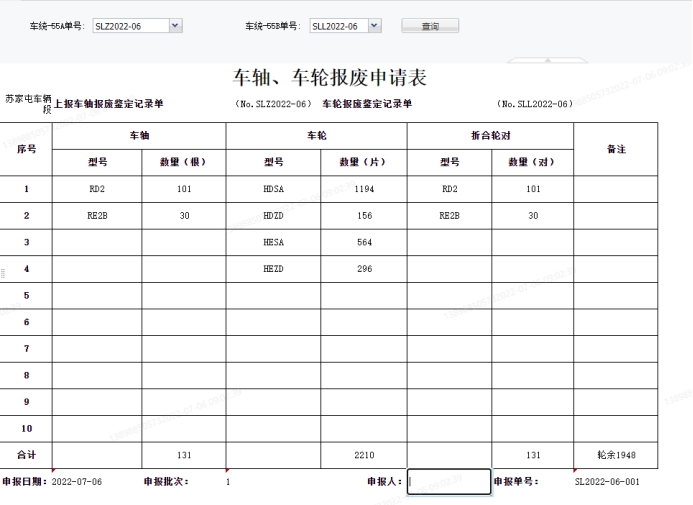
报废申请单
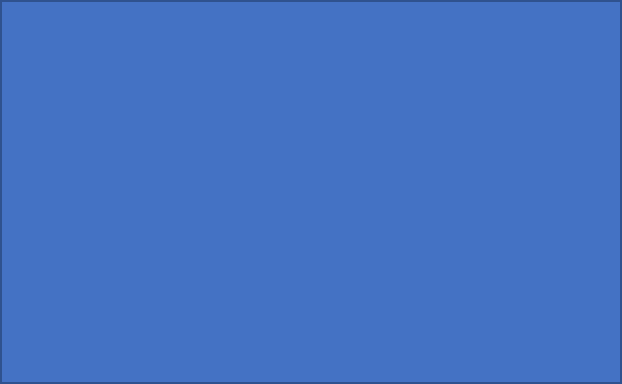 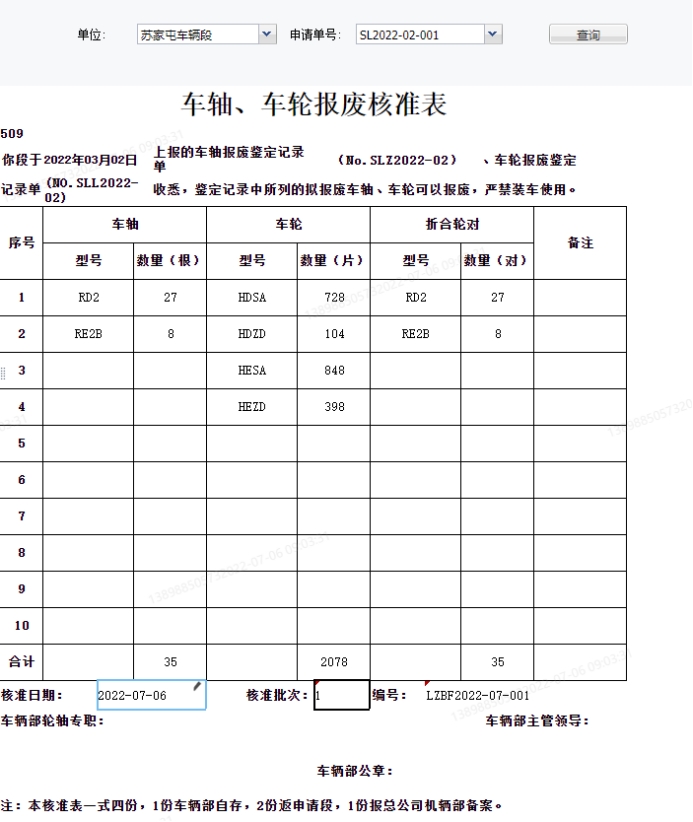
报废核准单
4.轮轴发送网上办理
调取生产流水线生成的轮轴、轴承发送信息和段内其他六个部门的装用轮轴数据信息,自动生成发送单。发送时间需要根据实际情况人工进行点选录入。接收部门在收到物品后,在网上办理接收。
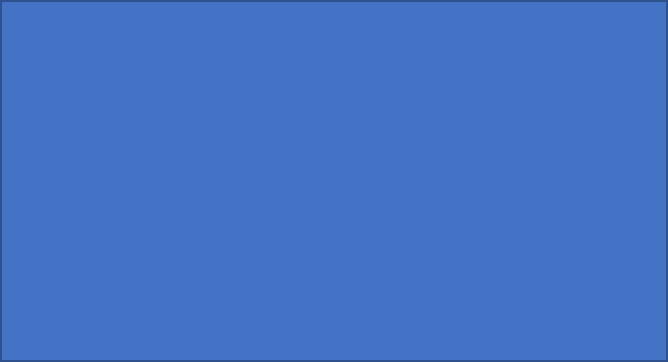 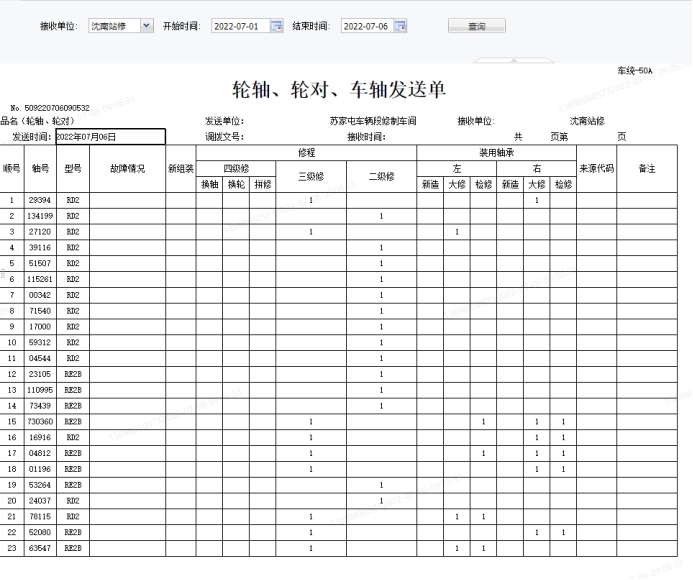
轮轴发送单
 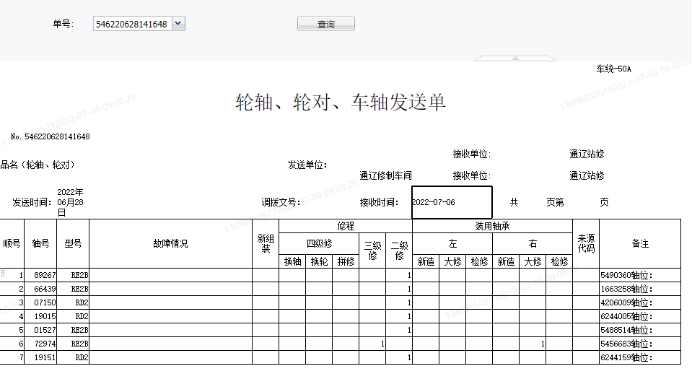
发送轮轴接收单
5.设备报修网上办理
设备发生故障时,现场工作者进入设备报修报表界面扫描设备二维码调取设备信息,点选设备故障表现,提交进行设备报修。设备维修部门由调度按照分工指派班组进行处理。处理人根据实际处理情况填写故障原因和处理结果,最终形成闭环。
 
故障报修单
 
故障处理情况反馈
价值:
1.实现了业务流程的闭环管理与过程追溯。
2.提高了业务流程的办理效率,大大减少了流程中的审批排队以及材料准备时间,以物料请领为例,减少了80%物料领取的等待时间。
3.实现数据共享,取消了数据的重复录入、采集。
场景三:自动统计分析
痛点:
原有的统计分析工作都是由各部门从系统中导出后进行人工统计,这种方式主要面临以下痛点问题:
1.取数困难且容易出错。业务人员需要把分散在各个系统中的或者各部门上报的数据通过EXCEL进行整理汇总,这项工作耗时巨大。许多报表的项点较多,在对数据进行整理过程中还容易发生数据整理错误的问题。
2.数据时效性差。许多周统计分析数据无法进行,月统计分析数据需要中旬才能完成,数据价值降低。
解决过程:
使用流水线数据、业务流程数据作为数据源,按照各个统计分析逻辑关系,开发自动统计分析报表。共开发流水线标准报表45张,设备报表4张,物料报表8张,财务报表3张,人员报表5张,合同报表2张。
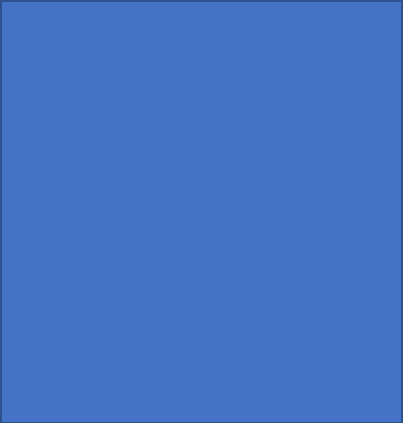 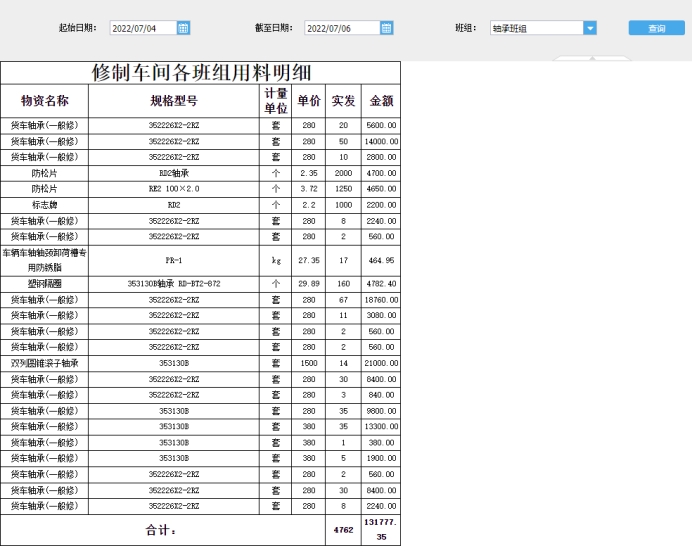
用料明细表
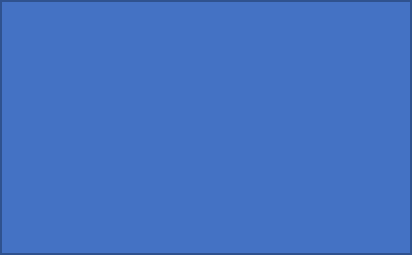 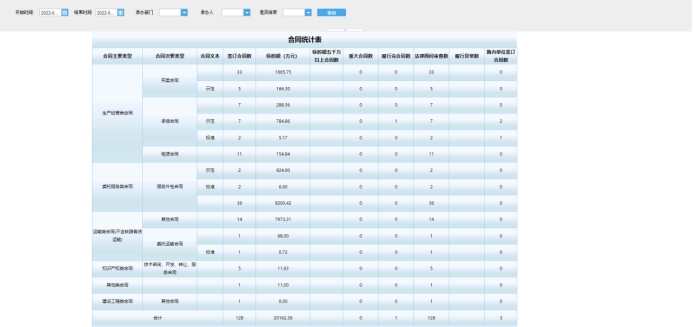
合同统计表
 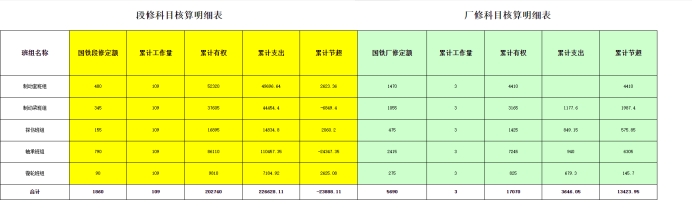
财务核算表
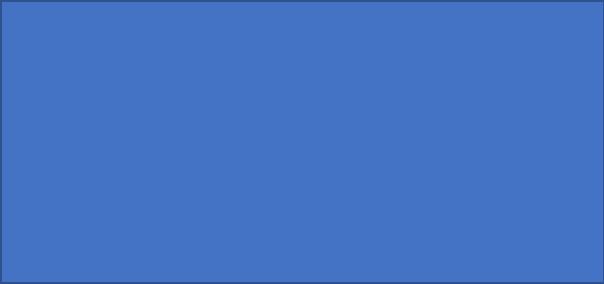 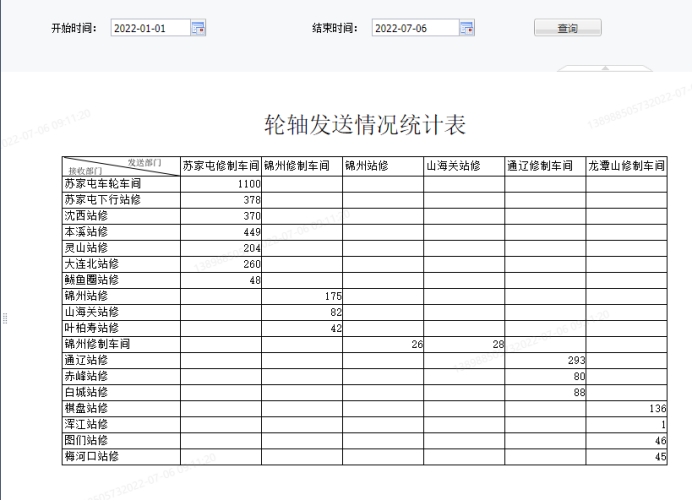
轮轴发送统计表
价值:
完全实现了统计分析自动化,实现了数据的实时统计分析,将人工统计分析工作量降低为0。
场景四:生产、业务流程的智能控制
痛点:
未使用系统前,需要人工对重要的生产环节进行确认,严重制约生产效率,还造成较大的人力资源消耗
1.生产作业需要对每个每个工件的前面所有工序进行一次确认才能够确定本工位是否进行作业,个别工位在确认上花费的时间要高于本工位作业时间。
2.车轮压装、轴承压装工位、轮轴选配工位每次都需要根据轮座、轴颈、钩高的尺寸现场选配匹配的车轮、轴承、轮轴工件,存在严重的耗时高问题,形成流水线生产瓶颈。
3.国铁集团公布的隐患零件的数量一般都在千条以上,每收入一条轮轴都需要人工在EXCEL表内进行一次检索,这样就需要设置一个专人进行此项工作。
解决过程:
1.按照工艺过程,根据生产数据确定单个工件的工艺流程,工作者扫码后即可确定本工位需不需要进行作业。
2.在轮座、轴颈、钩高工位测量完相关数据后,系统自动提示可选配工件的身份信息和具体数值,工作者按照提示信息选取即可。
3.将每次国铁集团发布的排查信息存入系统,在收入工位开发隐患排查界面。当收入轮轴信息包含在隐患排查信息内时,收入轮轴信息变红进行报警。
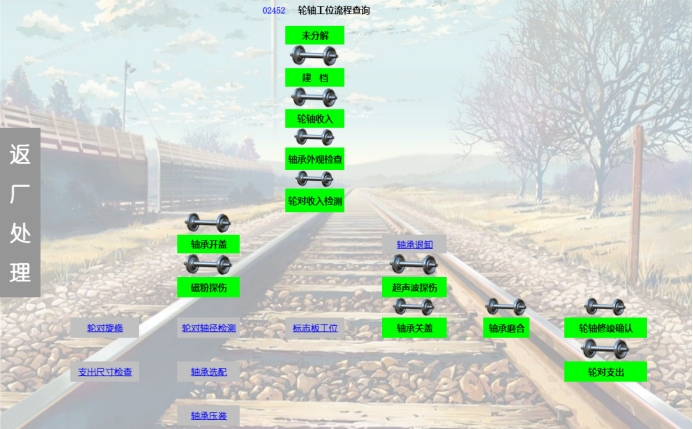
工艺流程自动控制
 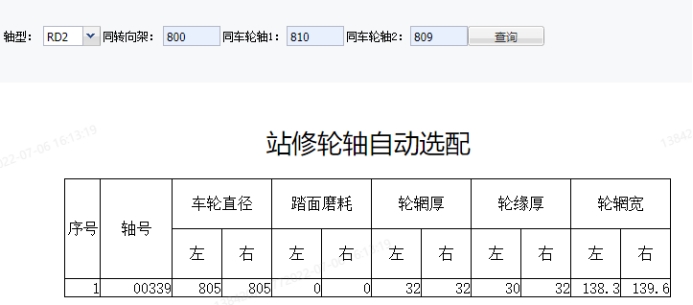
轮轴自动选配
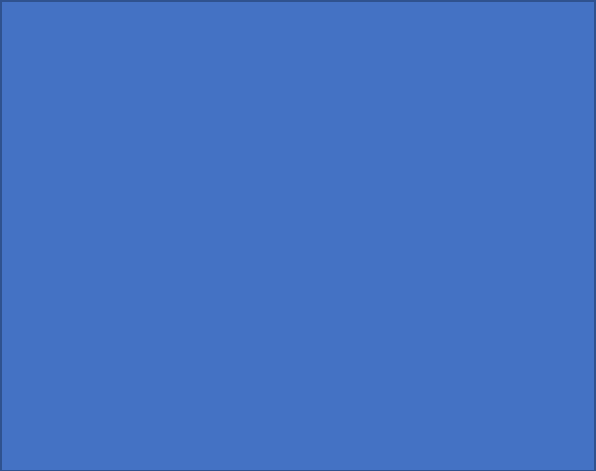 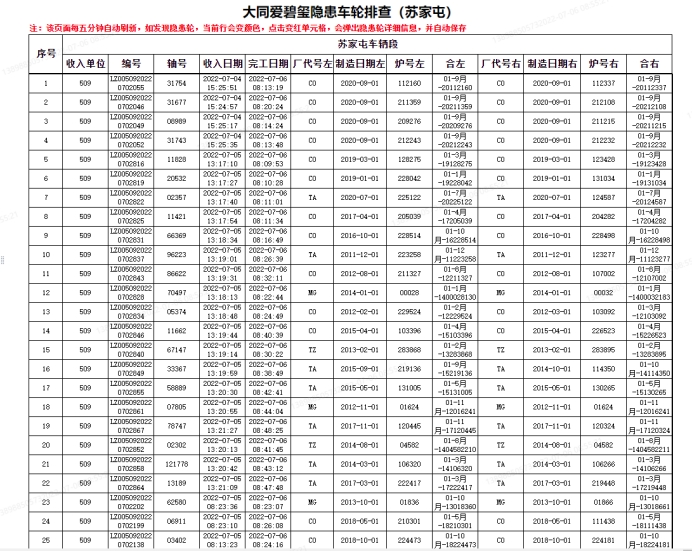
隐患配件自动排查
价值:
1.取消了各工位人工确认工件是否需要进行加工环节,现场整体生产效率提升15%。
2.取消了工作者在现场查看工件尺寸进行选配环节,只需根据智能选配提供信息直接调用配件即可,将选配环节效率提高90%。
3.取消隐患配件排查工位,为现场减少一个生产人员,每年节省工资性支出15万元。
场景五:可视化数据展示
痛点:
以往的数据展示多数使用PPT汇报的方式,统计分析多以简单表格方式进行,许多管理人员和生产人员关心的数据没有被展示。
解决过程:
首先我们进行了需求调研,分别与业务部门和生产部门进行沟通,确定了需要进行展示的数据。其次根据需求建立数学模型,我们对生产和业务数据源进行梳理,通过清洗、转化、加载对各数据源进行整合。最后我们确定围绕生产、物料、人员、设备四个方面开发看板。
1.工位生产任务数据大屏。
按照生产线开发了所有工位工作人员的每日工作量统计大屏。
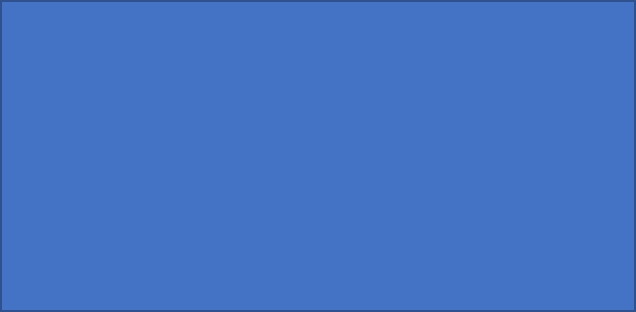 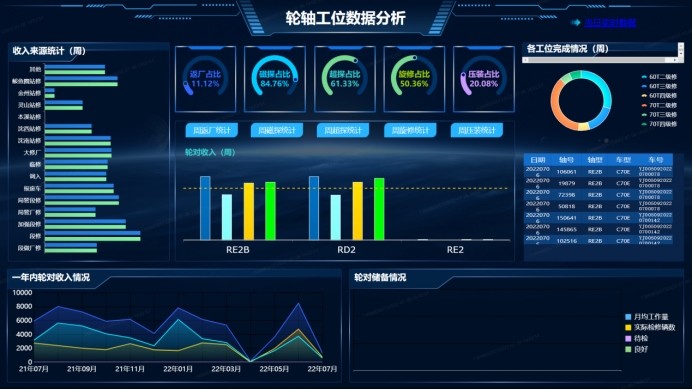
2.重点生产数据确认看板。包括轮轴收入岗位数据分析、轴承退卸数据、轴承一般检修数据确认、车轮旋修数据分析等。
       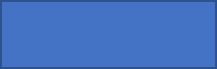 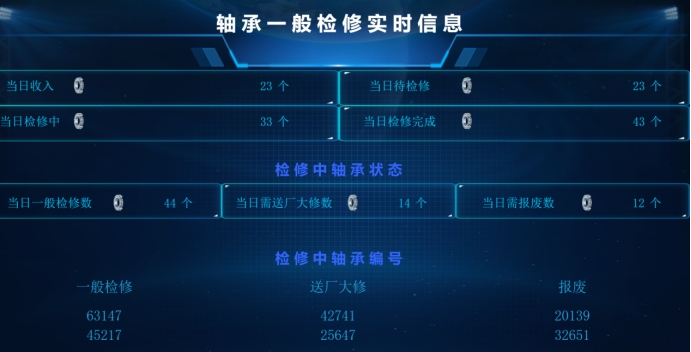
3.轴承生产数据大屏——轴承主要生产数据展示
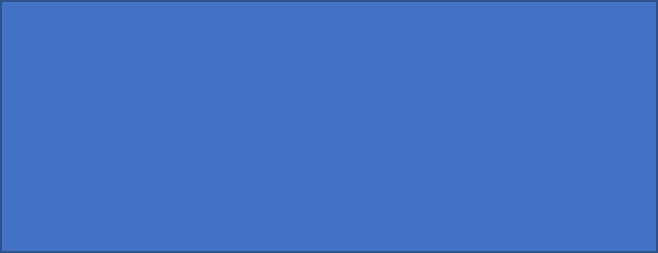 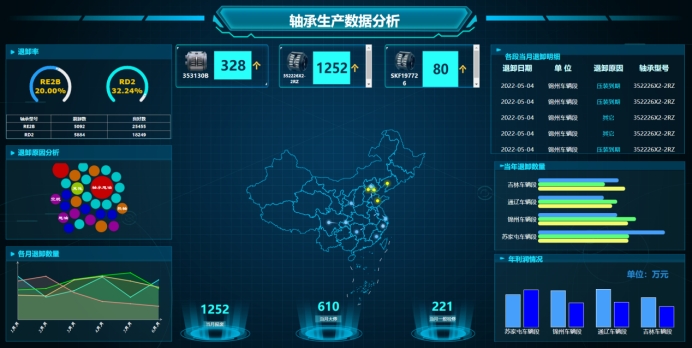
4.轮轴配件储备大屏——轮轴主要配件数据展示
    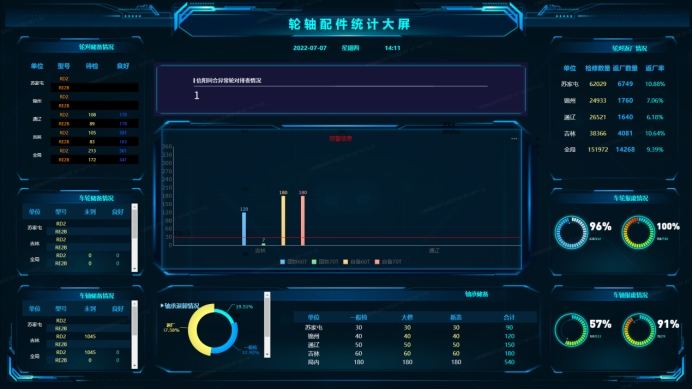
5.生产人员分析大屏——轮轴生产人员分析
 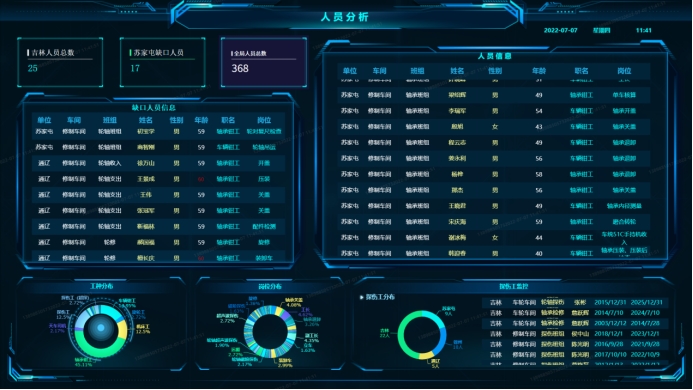  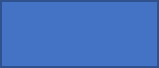 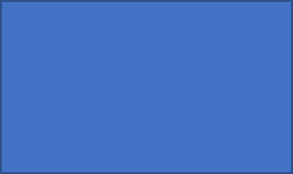 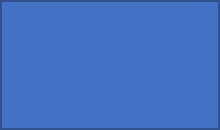
6.设备分析大屏——设备主要数据展示
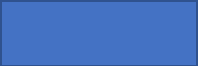 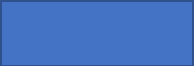 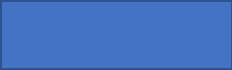  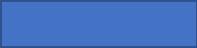 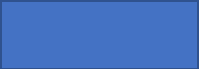 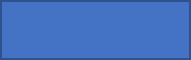 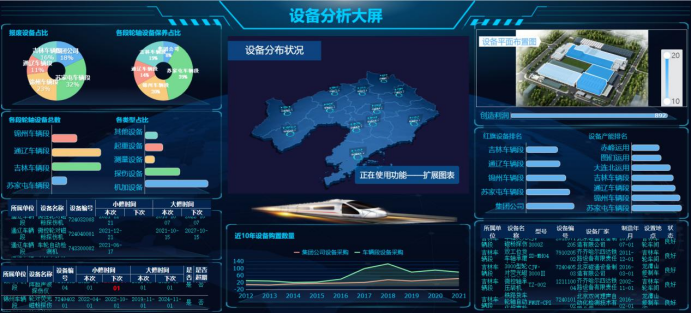
总结与展望
整个系统我们共开发报表226张,制作大屏23块。通过系统的使用,实现了无纸化生产流水线,我能直接减少了23个录入岗位,每年节省工资性支出345万元。实现了主要业务流程的信息化、数字化,然所有业务流程的办理过程都痕迹都能够长期保存,使问题溯源更加方便、准确。我们实现了统计分析的自动化,使繁重、复杂的统计分析过程变成了“一键查询”,将统计分析的人力资源消耗归零。实现了关键生产环节的智能控制,消除了人为漏放不合格产品的隐患。实现了主要数据可视化,让操作人员、管理人员都能够便捷的获得他们最关心的数据。
在这些已经实现的系统价值以外,让我们看到了自己开系统的无限可能。轮轴生产检修只是我们段业务中的一部分,目前我们正在研究将系统开发应用拓展至我们段的其他生产、管理流程。集团公司也确定将以我段为开发样板,在集团公司内的其他六个车辆检修单位进行推广。
目前我段在信息化、数字化建设方面取得的成绩,已经遥遥领先国内的其他铁路货车检修单位。国内的铁路货车检修单位的所有技术标准都是一样的,只是在工艺布局、工装设备等方面有些差别。我们所完成的系统开发,可以给全国的铁路货车检修单位提供了一个可复制、能操作的案例。 |