一、企业简介
北奔重型汽车集团有限公司(以下简称“北奔重汽”)位于内蒙古自治区包头市,创建于1988年,是中国兵器工业集团非承载轮式平台制造企业、军民融合型子集团。建厂以来,北奔重汽积极参与国家国防建设,服务国民经济建设,为国内国际客户提供整体解决方案。构建了NG80、NG08、NG09、NG10四大产品平台,通过先进的整车总装、驾驶室、车架、车桥生产线打造北奔精品,形成了“猛虎”、“蓝剑”、“奔马”三大子品牌,拓展丰富了自卸车、牵引车、越野车、特种车、新能源车和无人驾驶车等胜任全域环境的北奔产品谱系,成为了“国家企业技术中心”和“国家高新技术企业”。
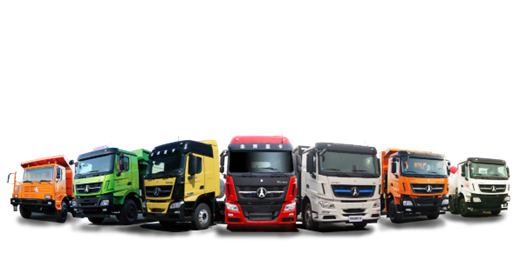
二、项目概况
结合公司产品特点和生产组织基础,搭建基于订单的准时化生产组织管理体系框架。将生产计划按照三级滚动计划管理模式控制,对各阶段订单进行分级管理,以计划排程为主线,采购计划与物流配送为辅线。围绕一级计划制定长周期物资采购计划,围绕二级计划开展MRP采购需求计划分析,制定短周期物资采购计划,实时订单跟踪、库存管理,围绕三级计划实施拉动式的准时化物流配送。梳理生产计划排程、采购计划、物流配送、生产作业四个环节业务痛点,重构核心业务流程。
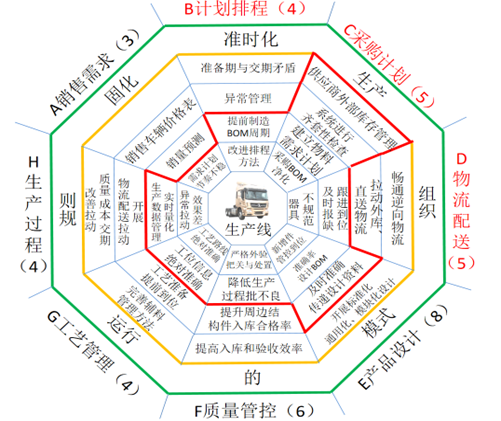
图1:主价值链核心业务梳理
通过核心业务流程的信息化与数字化建设,使生产过程更加平稳、有序、均衡,实现在需要的时间,生产需要数量的产品,交付需要的产品,以满足客户的不同需求,提高企业运行质量和市场竞争力。通过搭建数据流、掌握信息流、管住实物流,为企业落实“数智工程战略”,实现数字化转型提供了生产运营数据保证。
三、项目典型案例
场景一:准时化生产提升方面
痛点:公司在生产计划排程、物资需求及采购计划、物资齐套性检查、外部供应商及库存管理、物流计划配送、物料拉动等生产组织过程无信息化和数字化手段支持,各业务间各自作战无法深度协同,业务和数据不一致,影响生产组织的各类问题无一体化的信息系统进行集中管控。
解决方案:
(1)数字化赋能生产计划排程
计划排程管理采用三级排产方法,即一级计划是由销售需求计划转序生成的批次生产作业计划,一级计划只限定了整批合同的初步装配时间,上线时间可以随后续排产情况进行调整;二级计划是由一级计划转序生产的装配计划,二级计划相比一级计划,整批合同的装配时间更加准确,具体的装配时间仍可以根据实际情况进行小范围调整。三级计划是由二级计划转序生成的底盘上线顺序,三级计划限定了整批合同中的每一台车的上线时间和上线顺序,这一顺序是刚性的不可调整的,是拉动物流配送的关键数据。
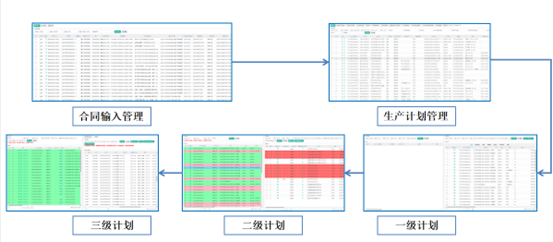
图2:基于订单的三级排产计划
(2)数字化赋能采购计划
物资采购部依据MRP运算结果和未完结订单制定的零部件采购计划,采购计划与生产计划的车辆型号及上线时间顺序紧密关联,采购计划制定后,按计划下达订单,并实施订单跟踪,向供应商发布物料需求计划看板,实时查看需求动态。
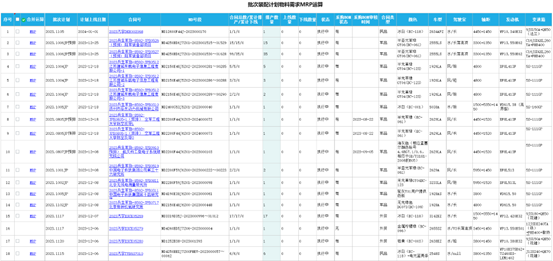
图3:MRP物料需求计划
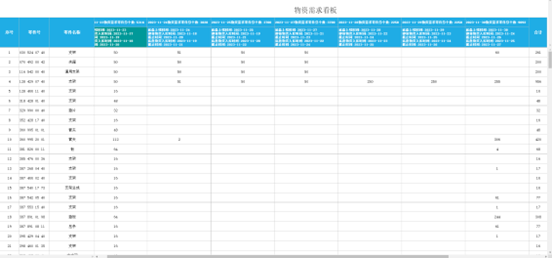
图4:物资需求看板
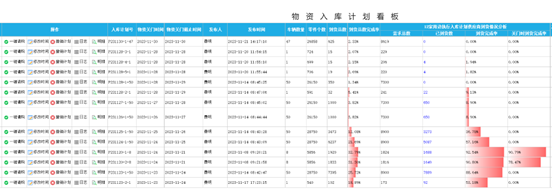
图5:物资入库计划看板
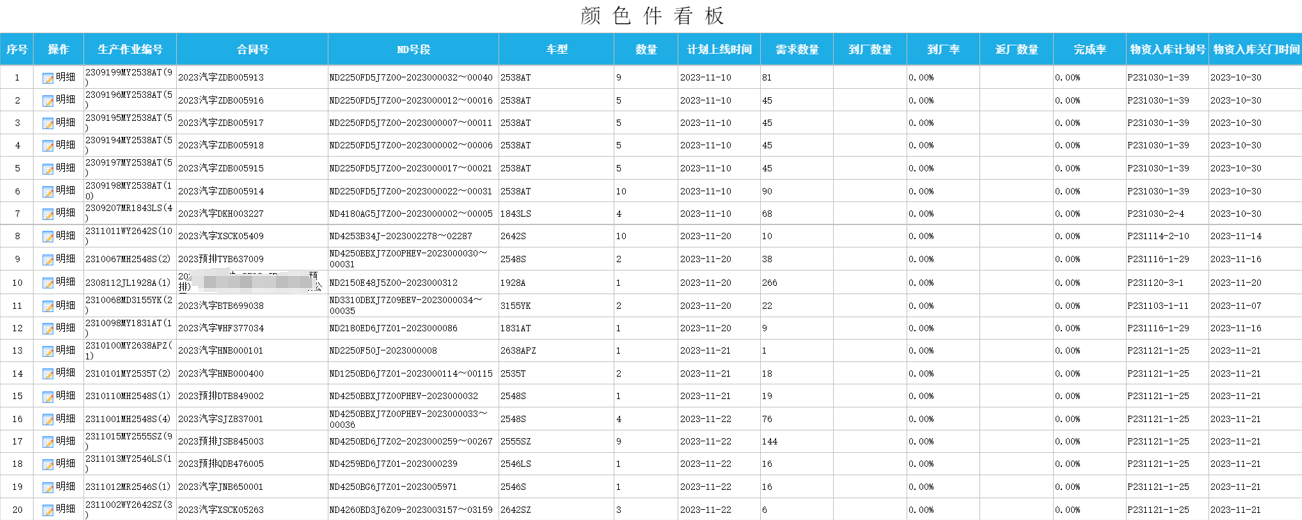
图6:颜色件采购看板
(3)数字化赋能物流配送
流配送按配送方式实现按序配送、提料配送和拉动配送。按序配送是指大部件按照上线车辆的顺序逐一、滚动配送并确认配送完结的配送方式。提料配送是指根据特定范围的工位或岗位提出的用料需求进行的配送,如预装工位、标小件以及生产、调试过程的临时用料。拉动配送是指按照在线车辆及待上线车辆的顺序,根据采购BOM自动生成配送计划而进行的配送。配送业务利用二维码进行数据传递和确认,并在业务看板上指导配送及管理人员查看完成情况。
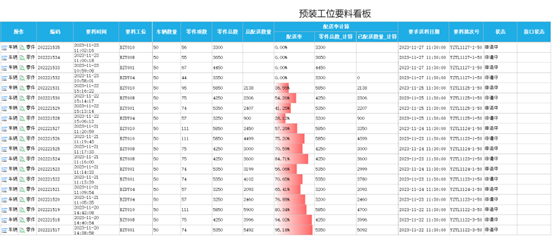
图7:预装配送管理

图8:底盘配送管理
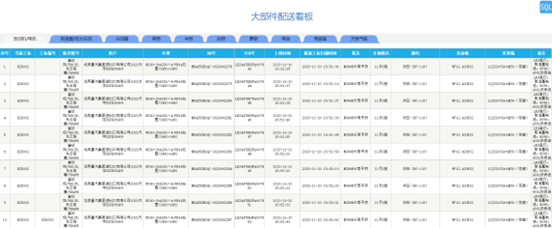
图9:大部件配送管理
(4)数字化赋能生产管理
基于三级计划,开发虚拟的生产运行看板,实时查看车辆在线流动情况和生产运行停止的状态。利用工位机的工位看板,实时发布缺件、质量、工艺、设计方面存在的异常。按工序流程设置数据采集点,实时掌控各工序完工时间,形成基于合同的履约进程数据管控平台。
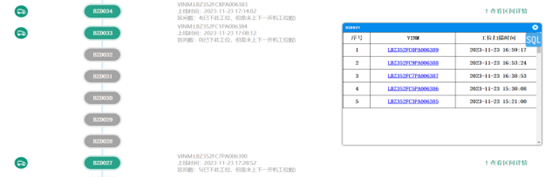
图10:生产运行看板
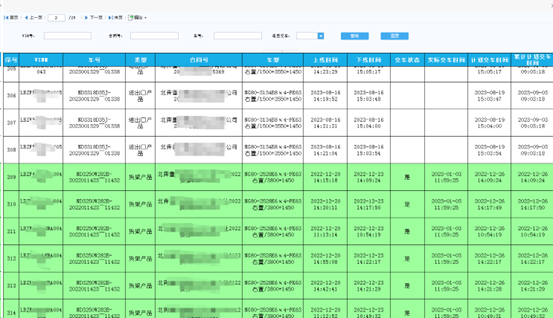
图11:车辆履约交付全过程管理
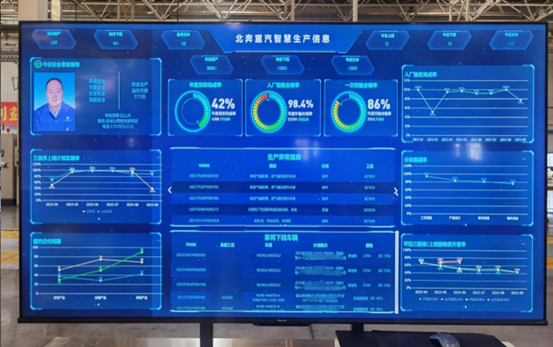
图12:总装智慧生产信息大屏
引入直通率质量管理工具实施动态考评,实时展示底盘线每道工序的通过率,以及产品设计、零件质量、物料准备、工艺制造等分项指标完成情况,推动异常问题的快速解决,为准时化生产提供支撑。
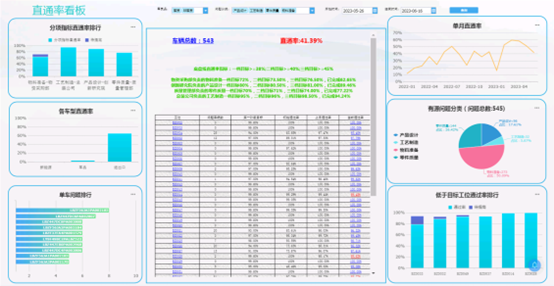
图13:生产履约组织过程直通率数据价值创造
实时查看异常停线的工位、工序及启停时间,利用统计分析数据找出影响生产线连续运行的工艺问题或物料问题以及质量问题并加以优化,提高设备可动率。

图14:异常停线数据看板
成效:生产计划排程方面:计划完成准确率可提升至 90%以上,排程调整时间缩短 50%以上;物资需求及采购计划:采购计划与实际需求的匹配度达到 95%,采购周期平均缩短 20%;物资齐套性检查:齐套率能稳定在 90%以上,因齐套问题导致的生产延误减少 80%;外部供应商及库存管理:供应商准时交货率提升至 95%,库存周转率提高 30%;物流计划配送:物流配送准确率达到 98%,配送及时率提升至 95%;物料拉动:物料拉动的响应时间缩短 40%,缺货率降低至 5%以下;协同方面:各业务间协同效率提高 70%,信息传递延误减少 90%;业务和数据一致性方面:业务与数据的一致性达到 99%,数据纠错成本降低 80%;整体生产组织:生产效率提升 40%以上,生产周期缩短 30%,成本降低 20%。
有了这些具体指标的提升,公司的生产组织将更加高效、有序,能够更好地应对市场变化和客户需求。
场景二:生产履约能力提升
痛点:公司在长期的运营过程中积累了海量的生产数据,但缺乏与之对应的相关指标来对其进行有效的管理和提升履约能力。
履约能力,对于公司的持续发展和市场竞争力至关重要。它关系到我们能否按时、按质、按量地完成客户的订单,能否在市场中树立起可靠的信誉和形象。没有明确的指标来衡量和引导,我们无法确切知晓生产流程中哪些环节可以进一步优化以缩短生产周期,无法精准地判断资源的调配是否合理以确保高效生产,也难以找到提升产品质量和稳定性的关键突破点。这使得我们在面对履约压力时,常常感到力不从心。
解决方案:梳理核心业务流程约束性管理需求,制定各类生产履约指标算法,开发“生产系统作战指挥平台”,实现指标数据的自动采集和分析统计,以数据看板形式呈现给现场管理和技术人员,引导业务的规范开展,构建“生产数字化运营指标体系”。形成了包括指挥平台21项指标和内容、月度评价6项指标和内容、出库效率评价4项指标和内容、履约周期评价10项指标和内容、内部潜在2项指标和内容、销售大纲符合度评价4项指标和内容、零件主数据8维度综合查询报表、履约进程综合查询报表、自制件齐套率评价看板、扫码统计5项指标和内容、排产计划执行综合查询报表、新产品开发进度综合查询报表和标准件对照使用手册综合查询报表在内的“数智化赋能生产履约全过程”的“数据分析展示平台”。
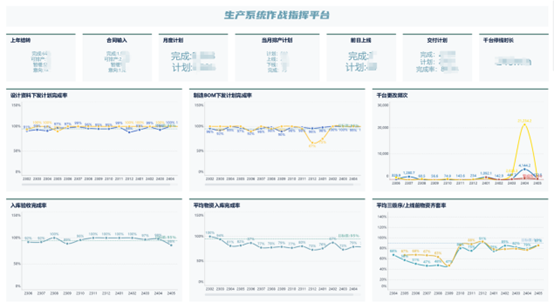
图15:生产系统作战指挥平台
图16:生产系统作战指挥平台
开展生产履约单位综合性评价及专项业务评价,搭建围绕生产履约五个阶段+六种评价的管理体系, 包括生产履约工作综合评价、出库效率评价、履约周期评价、内部潜在损失评价、销售大纲符合性评价、自制件评价等内容,最终通过数据推动业务管理能力提升。
生产履约工作综合评价用于评价业务单位综合管理水平和生产履约工作质量,每月编制评价报告并在调度会通报。销售大纲偏离度用于评价合同输入指导性,指导公告、技术、工艺、物料的准备工作。风险项辨识与生产前准备状态成熟度用于评价准备充分性,提前识别风险项,不具备生产条件的不安排生产,减少仓促上线带来的异常问题。潜在内部损失用于评价工作质量,按单位统计合同变更、设计资料错误、生产缺件、零件质量问题带来的工时及材料费损失,督促工作质量提升。履约周期用于评价交付及时性,找出履约周期不达标的车型,梳理影响因素提高履约效率。出库效率用于评价履约精准性,督促交付不出库而形成资源占用的改善。
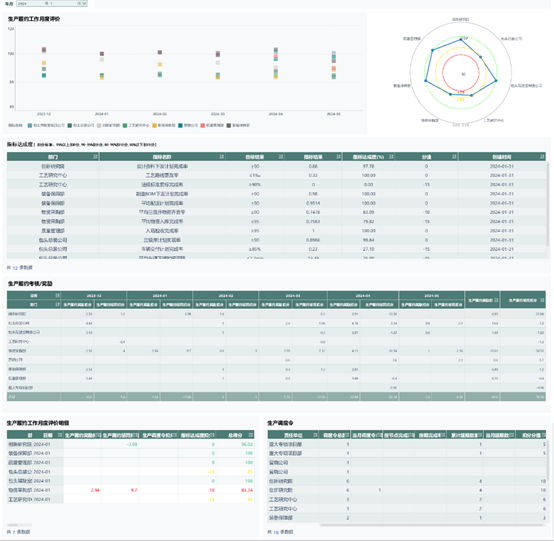
图17:生产履约工作综合评价
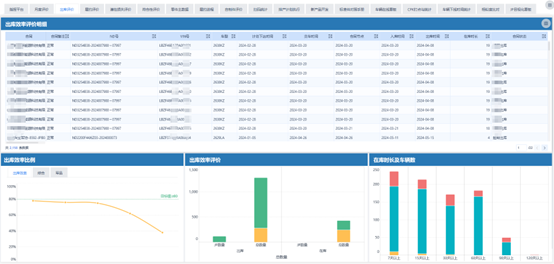
图18:出库效率评价

图19:履约周期评价
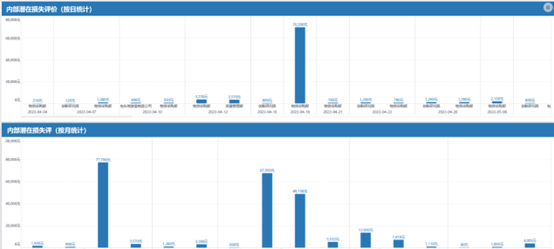
图20:内部潜在损失评价
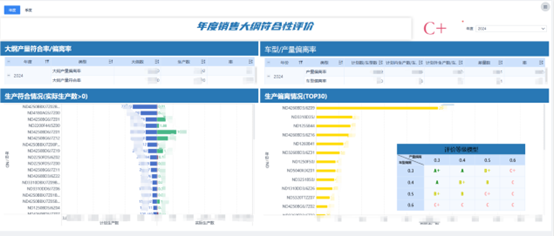
图21:销售大纲符合性评价
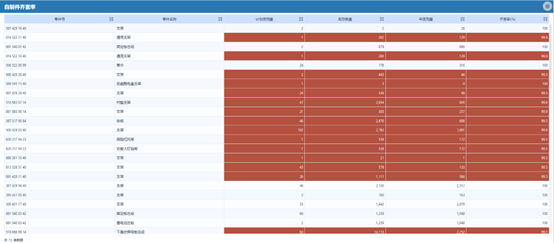
图22:自制件评价
成效:通过建立从设计输出到车辆交付过程关键节点的准时化指标体系,实现全系统数据的看板管理,及时、透明地展示生产组织运行情况,一键查询影响21个关键指标或未达到指标要求的问题,通过数据推动业务改善,有效支撑生产履约能力和业务精细化管理提升,创造“数据价值”
场景三:物资入厂齐套率提升
痛点:准时化生产项目实施前,公司在生产组织、物资需求和采购、物流配送等业务环节无有效信息化手段支撑,物资入厂齐套率全靠人工识别跟踪。
解决方案:“以问题为导向,最小化投入” 在U8系统的基础上扩展移动化WMS系统,数字化、流程化、分段管理,以U8系统为数据中心结合准时化生产物流拉动模块,形成数据接口,实现全流程透明化、可视化、标准化、精细化管理,向智慧物流转型升级。
在现有信息化平台的基础上对生产制造业务领域上下游业务进行流程梳理,根据业务需求进行数字化改造。利用FineReport自主开发为主现软件功能开发工作。
(1)开发智慧物流APP,实现物流核心业务的移动化
通过对物流核心业务数字化、流程化和分段管理,结合准时化生产组织模式完成到货办理、入库办理、到货提验、配送拣货、大部件确认、JP集件和标准件物料卡等功能模块开发。
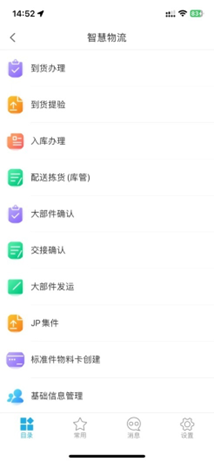 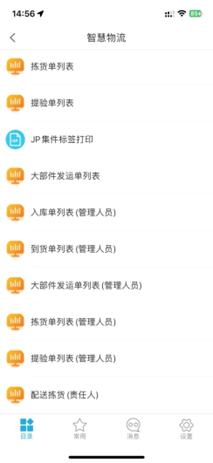
图23:智慧物流APP首页
在现有准时化拉动的基础上,开发供应商发货单功能,发货前供应商须在供应商协同平台制作“北奔重汽供应商发货单”,并打印,到达公司库房后先通过移动端APP扫码快速确认到货,并提交质检 。通过ASN发货单(入库交接单)的形式提前掌握供应商发货情况,实现到货计划看板、来料校验计划看板。通过标准化单据支撑来料检验、入库业务的快速化。
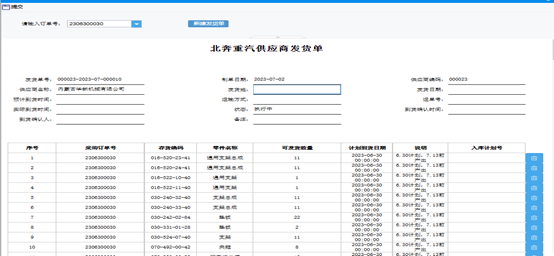
图24:供应商发货单
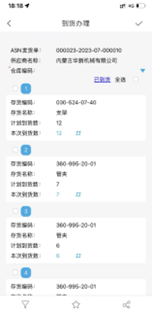
图25:到货办理
流程化、看板化质检:通过ASN发货单生成来料校验计划看板,拉动质检。通过标准化单据支撑来料检验,未检验无法办理入库、出库手续。
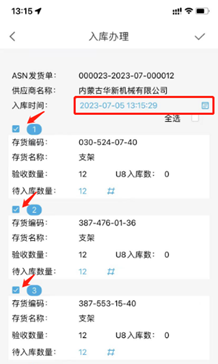
图26:入库办理
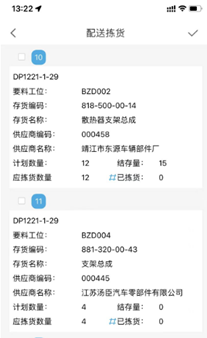
图27:配送拣货
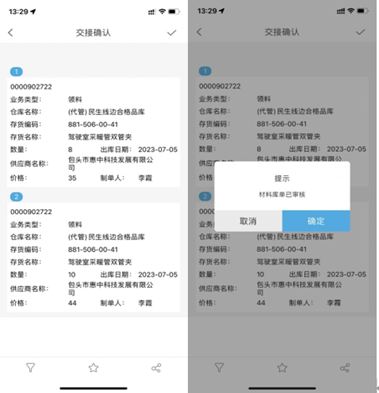
图28:交接确认
移动化拣货出库交接:通过现场大屏看板拉动、移动化App端实现拣货指引、快速备货。物流现场设置打印机,实现快速打单出库。移动化扫码快速接收确认。
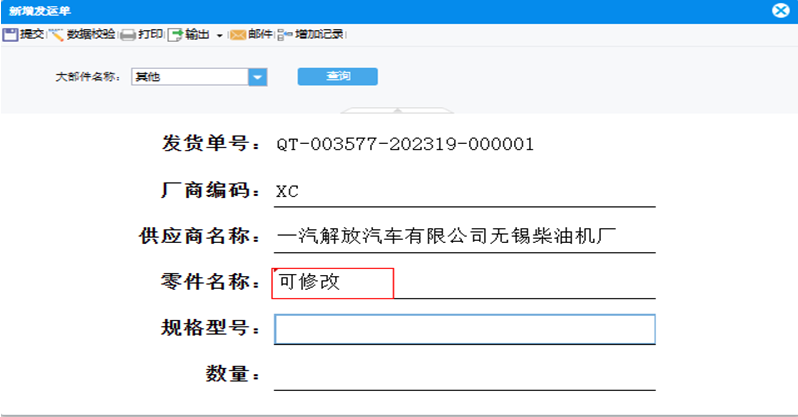
图29:大部件发运单创建
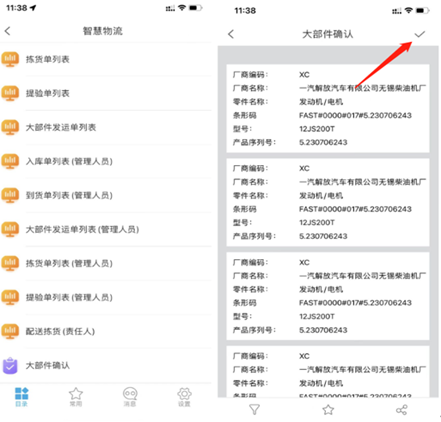
图30:大部件确认
成效:构建了在制造领域与上下游建立更紧密的流程衔接,更有效的对库存、合同、采购进行跟踪,管理、分析。增强对制造领域的可视化管理;构建体系完整、架构清晰、流程顺畅、责任明确、运行高效的业务信息化管理体系,提升业务运转效率。优化业务流程提升效率,拉动产品设计、工艺管理、采购计划、物流配送等关键环节,实现合适的时间、合适的数量、合适的产出。
建立了较为稳定的生产秩序后,固化准时化生产组织模式的运行规则。产线直通率可以提升,产品下线的合格率会提高,交付的节拍会缩短,过程的成本会减低。
四、项目总结与展望
准时化生产组织体系对计划排程、采购计划、物流配送等核心流程优化,让生产更平稳、有序、均衡,可在特定时间生产特定数量产品并交付,满足客户多样需求,提升企业运行质量与竞争力。面对单台 2600 余件专用件及 400 万次月物流量,实现生产物料需求与供应链物料准备的数据、信息、实物协同,解决物料需求预测偏差 8%、采购订单延迟 10%、发货到货跟踪难等问题。建立动态物料齐套率算法,解决计划排产信息不全面不准确、排产不稳定、合理性不佳等难点。稳定生产需稳定准时化物料配送,建立多形式配送模式,解决了紧急拉动配送频繁问题。及时准确数据查询及看板查看是关键,解决人工统计及时性差(延迟 15%)、准确性低(偏差 6%)、规范性差、重复工作量大等问题。
后续要不断改进准时化生产组织体系,进一步提升生产的平稳性、有序性和均衡性。进一步挖掘生产运营数据的价值,通过数据分析来发现更多潜在问题和改进机会。
利用数据进行精准预测和决策支持,提升企业运营的科学性和前瞻性。加强员工在准时化生产理念和技能方面的培训,确保全员理解并能有效执行。运用数据监测和分析来及时发现质量波动并采取措施。建立完善的监控指标体系,定期评估各项改进措施的效果。
|