数字化分析决策平台助力企业精细化管理提升
一,企业介绍
徐工集团徐州重型机械有限公司(以下简称“徐工重型”)是徐工集团核心企业,主要研发、制造、销售汽车起重机、全地面起重机和特种起重机,拥有较为全面的产品型谱,包括8吨-220吨汽车起重机,100吨到全球最大的2000吨级全地面起重机,25吨到150吨越野轮胎起重机,能为全球客户提供全套化吊装解决方案。产品市场占有率超过50%,营业规模超过200亿,产品销售至包括欧洲、美国、澳大利亚、韩国、巴西、阿根廷等全球187个国家和地区,连续14年全球销量第一。2020年,经权威机构综合评测,徐工重型力压世界巨头德国利勃海尔,位居全球移动式起重机排行榜第一名。
徐工重型是中国流动式起重机分标委秘书处承担单位,工信部智能制造能力成熟度评估行业内首家达到四级水平的企业,连续两度登上国家《大国重器》舞台,2014年、2018年,两次荣膺中国工业大奖。徐工重型先后被授予国家“智能制造标杆企业”、“制造业单项冠军企业”、“中国工业行业排头兵企业”、“中国工业先锋示范单位”、“中国重大技术装备首台(套)示范单位”、国家级“两化深度融合示范企业”等荣誉。
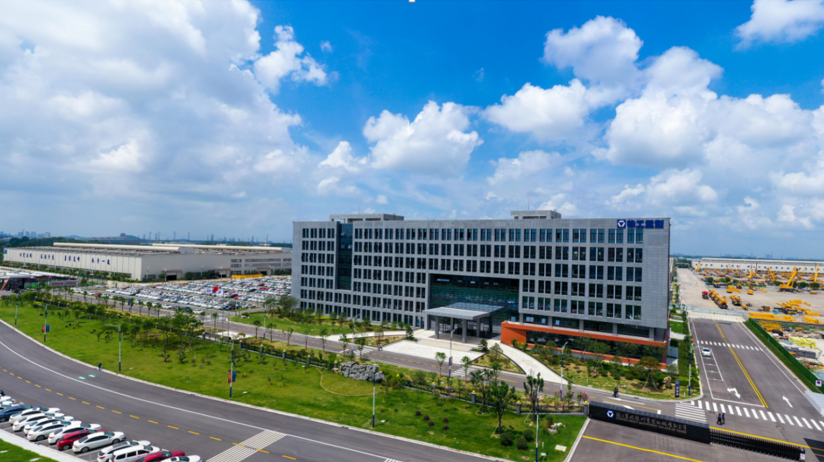
企业形象图

企业logo图
二、项目背景及意义
徐工重型先后建设了ERP、PDM、MES、SRM、CRM等几十项核心信息系统,实现了信息化在研发设计、生产制造、采购物流、营销服务等各环节的覆盖和应用。但随着信息系统数量增多、业务功能的复杂和交叉,企业产生了TB级的业务数据,一方面业务数据质量参差不齐,另一方面业务部门间存在“数据应用壁垒”,导致数据资产不清晰,分析部门获得不到数据,或者获得的数据是掺杂了大量无效的数据,无法有效支撑企业进行数据分析和决策。
徐工重型提出“数字化转型战略”,通过实施数字化分析决策平台,实现不同领域、不同维度下业务的全方位挖掘分析,分析数据背后的价值,发掘管理痛点,打破数据壁垒,细化管理维度,提升管理效率。
三、项目解决方案
1)建设数字化分析平台
公司与帆软公司联合,成立了以公司总经理牵头挂帅,以业务部门为主体,以信息化、帆软技术专家为技术引领的专业化团队,并建立数据分析项目小组,着力培养公司内部数据分析人才。项目组对关键核心业务应用和数据现状进行调研,并对每项核心业务数据分析的可行性进行了评估。项目规划了数字化分析运行平台建设框架,按照纵向到底、横向到边的原则,纵向划分为公司级、分厂级、区域级三级分析层级,横向制定研发、生产、服务、营销等十多个分析模块,全方位覆盖公司业务范围。依据“全局规划,局部推进”的方法,以服务模块为试点中心,细分集团级、公司级和个人级任务统计指标,规划形成了整体业务纵向细分至个人,横向落实至指标的分析路线。同时在生产、设备、营销、人力资源等方面,根据需求搭建示范场景,可对外提供各种分析监控手段,保证管理的精细化管控。
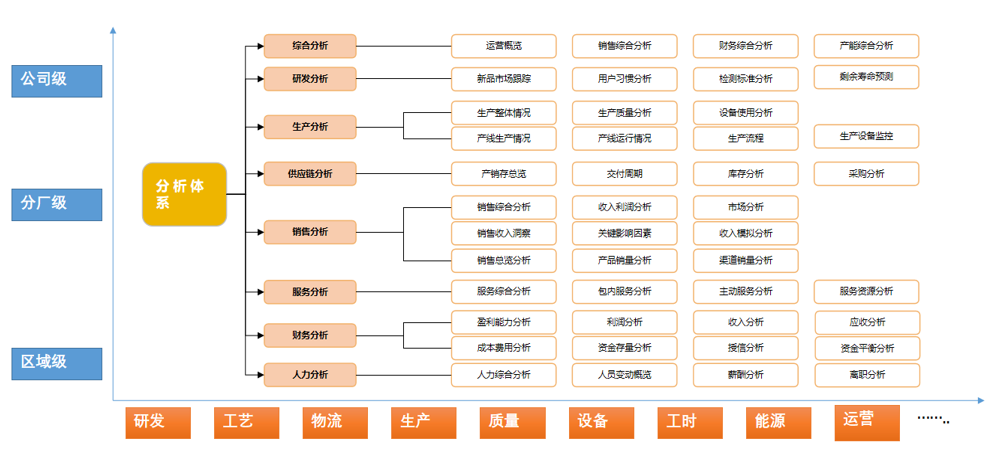
图 数字化分析运行平台建设框架
2)搭建企业级数据仓库
构建统一的数据仓库,实现对不同源头、标准的业务数据进行集中的管控与处理,保证数据的质量与安全。数仓建设分为数据源抽取阶段、数据清洗处理阶段、数仓存储阶段和数据应用阶段。
数据源抽取阶段:需要根据具体业务抽取局部数据,在保证分析维度及时效的前提下制定数据抽取策略及频次方案,保证底层数据的及时更新。
数据处理及清洗阶段:使用Finetube工具,依据多源底层核心业务数据库的特性和业务对数据维度、时效、速度、容量等要求,制定管道级、数据任务级、定时任务级的三级抽取方案,维护数据的高效清洗及计算。
数仓存储阶段:使用Finedata工具,搭建分布式数据仓库,部署分布在不同物理机上的主从节点,通过主从机的高效协同实现了海量数据的高速计算和快速存储。依据数据分析维度,建立数据仓库三级模式,实现业务主题数据集市,为整合应用阶段提供强有力的数据支撑。
数据应用阶段:使用Finereport软件对数据集市中的结果进行分析应用与可视化的展示,进行维度建模,设置预览权限,确保不同角色的人看到不同粒度的数据,保证维度数据安全性;建立预警机制,设置异常问题推送规则,异常问题及时推送至主要责任人,保证异常问题及时得到关注并解决。
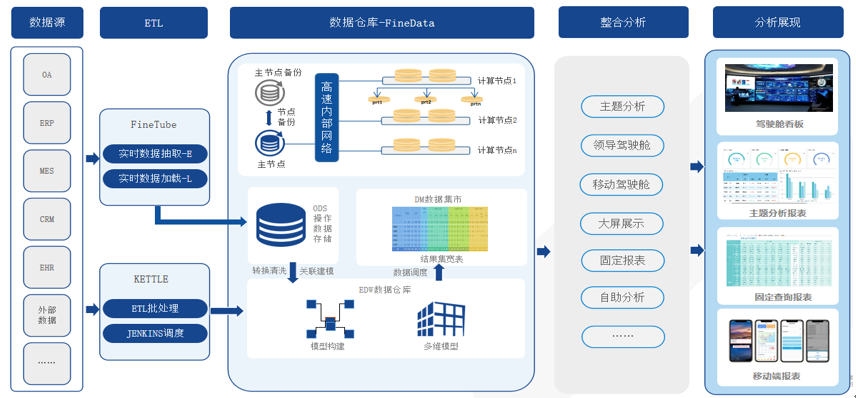
图 数据仓库架构
在实施过程中,我们也发现不少问题。其中最为突出的是数据治理,依据调研结果,现阶段业务数据存在的问题主要有两种:(1)数据分析思路变化过快,缺乏中长期主线,无法固定;(2)数据维度多样,但数据交互方式单一。每种分析思路及维度的变化都可能导致由底层数据到业务逻辑,自低而上的变更,会消耗大量的人力及物力资源。因此,后续发展过程中数据治理需要特别关注。
四、项目典型案例
场景一:服务快速响应
痛点:制造业的重心往往放在生产、营销、供应链,很容易忽视售后的服务效率与客户满意度,因此难以保证售后服务的质量与效率。如何解决服务网点、人员、备件等资源布局的合理性以及如何快速响应客户服务需求,是企业提升服务精准性和敏捷性的关键所在,也是企业构建长期竞争优势的一大要点。
解决方案:通过建设服务模块的数据分析试点平台联合远程运维服务平台、客户关系管理平台CRM、备件协同管理平台PMS以及呼叫系统,建立服务满意度、十分钟响应率等212项服务指标,充分利用服务数据分析结果最终实现客户精准服务、服务网点人员备件监控等资源精准布局的服务。依托数据仓库及业务需求,将服务业务划分为服务指标分析、客户投诉指标分析、预警分析、备件分析、流程中心五个板块,完成服务业务的横向拆解。
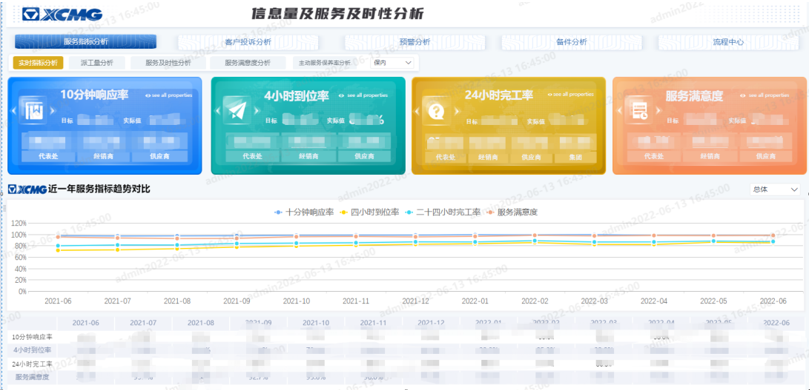
图 大数据服务资源分析模块
对服务指标分为实时指标分析、派工量指标分析、服务及时性分析、服务满意度分析、主动保养率分析5大模块121项指标体系,每个模块都完成自上而下、由本部到网点到个人信息的深度挖掘,实现了服务信息的纵向贯穿。
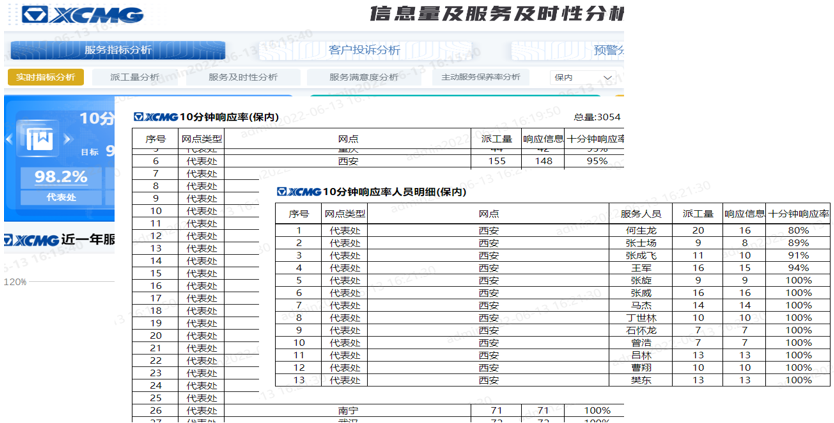
图 服务指标分析体系
客户投诉分析主要分为客户投诉及客户纠纷两个模块,通过对客户纠纷及投诉信息来源、地区及原因的分析,了解各城区、各代表处在客户服务方面存在的优缺点,辅助管理人员深入了解客户需求、灵活调整管理方案。
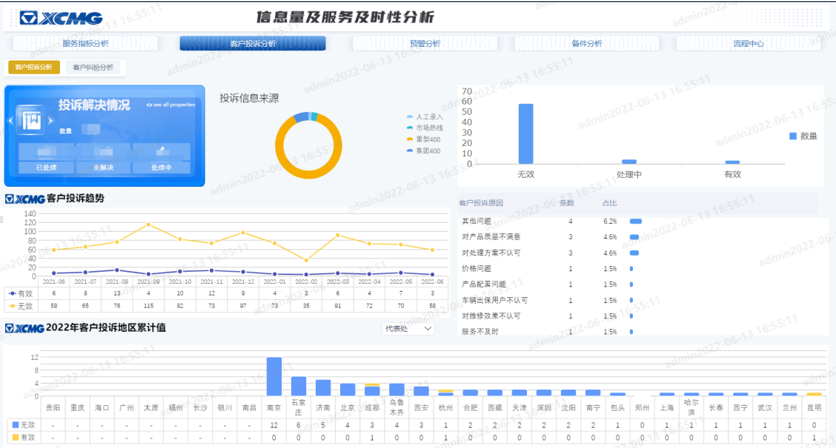
图 客户投诉分析
在预警分析中,建立预警升级机制,针对派工、内部联、备件满足等关键性指标设置预警规则与阈值,超出最大允许期限被认为业务延误,依据超出天数,不同的天数会以钉钉通知的方式提醒相关责任人,延误时间越长,通知的相关责任人职级越高,以此来倒逼管理优化升级。
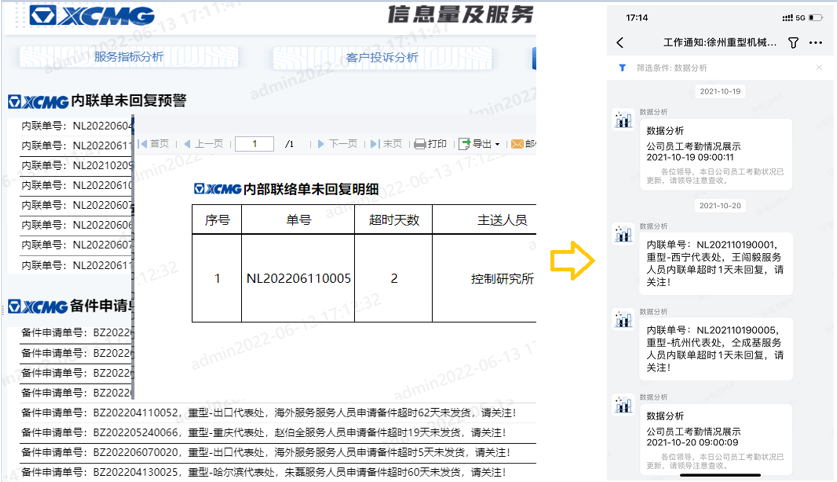
图 预警分析
备件分析主要以各地区、仓库备件的备件满足率及发运的及时率指标为主,主要的目的是可实时监控各地区仓储备件资源,分析不同地区对当地仓库建设的必要性、对不同备件的需求区间等因素以期达到备件资源的动态布局,实现对客户的敏捷服务。
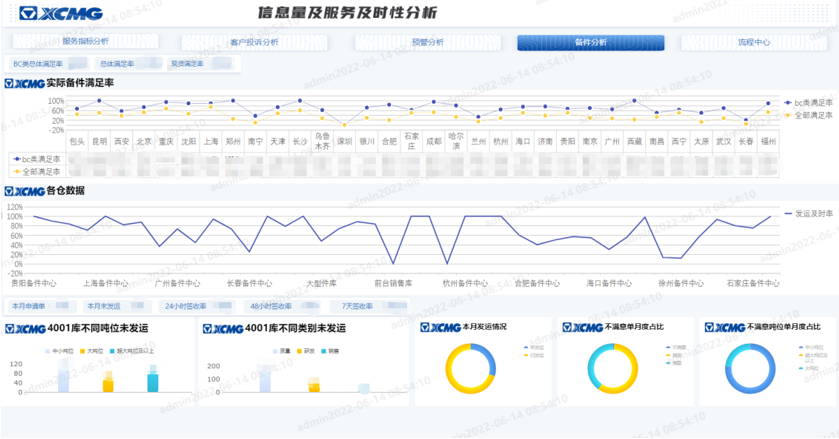
图 备件分析
流程中心是对各部门效率的一个监控指标,通过对各流程审批效率、延误时长的分析对比,减少各部门之间的交流成本,提升工作效率。
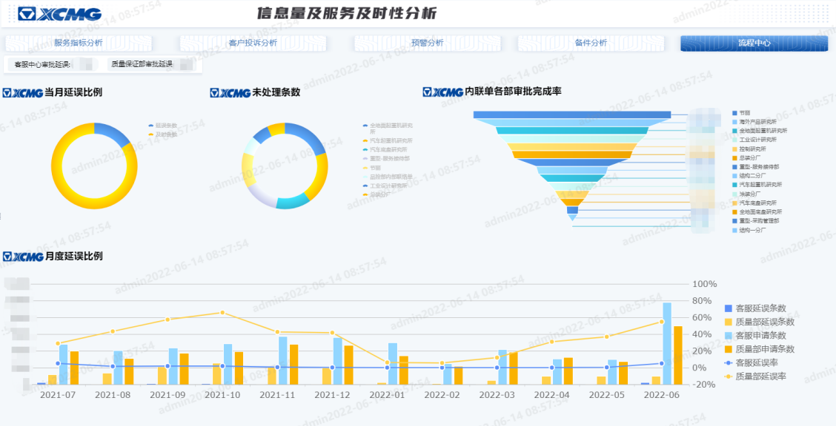
图 流程中心
成效:穿透式服务体系的实施使得服务分析周期由7天缩短至1天,效率提升85%以上。快速定位业务瓶颈点,实时透视服务数据,本部与代表处的沟通成本降低50%以上。服务指标中到位率提升5%,完工率提升2%,直接提升市场服务口碑客户感知满意度提高2.53%,客户投诉率降低5%,服务及时性提升4.73%。辅助核心信息系统在一机一册制作及查询准确性上提高至99.9%;客户备件/图册查询时间缩短70%。
场景二:生产资源动态组织
痛点:工程机械行业具备多品种、小品量、柔性制造特点,公司核心生产工艺的工序高度离散,由于生产过程数据不透明,生产过程中物料、设备、人员、场地等资源分配的不均衡、计划的不合理、报工的不及时都会造成不同程度的资源浪费,从而影响生产效率,导致无法对资源进行动态规划。
解决方案:
(一)构建生产驾驶舱
以SCADA、MES、WMS、QMS及APS系统为主搭建徐工重型生产驾驶舱,对公司整体的设备利用情况、生产计划情况、生产工时情况、产品质量情况、人员效率情况等数据进行综合分析,辅助管理人员快速了解生产的整体进度,合理安排各类资源,精准把控任务进度,提升生产效率。
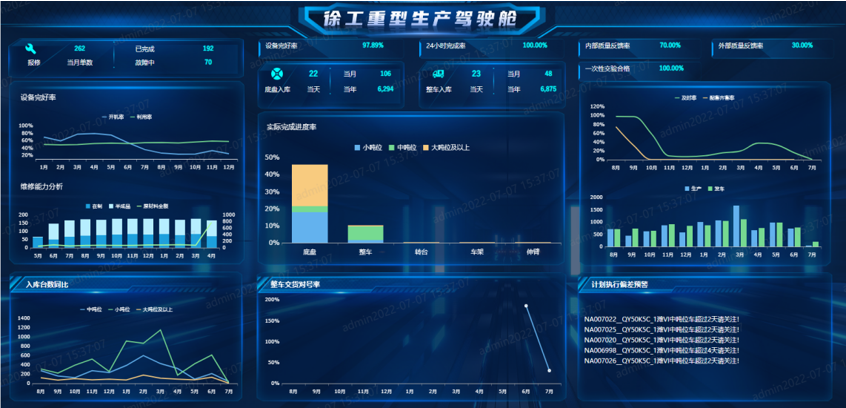
图 徐工重型生产驾驶舱
(二)构建多维分析模块,细化驾驶舱分析指标
设备分析模块:通过SCADA系统获取设备信息,并利用Finereport构建设备分析看板,对型号、数量、加工参数信息、设备两率、设备实时检测数据、设备联网情况、设备告警数据、设备预防性维护等多个模块进行实时监控与分析,结合MES系统的员工工时数据,分析员工与设备之间的“忙闲”状态是否匹配并进行适当调度,从而实现资源的统筹调配。
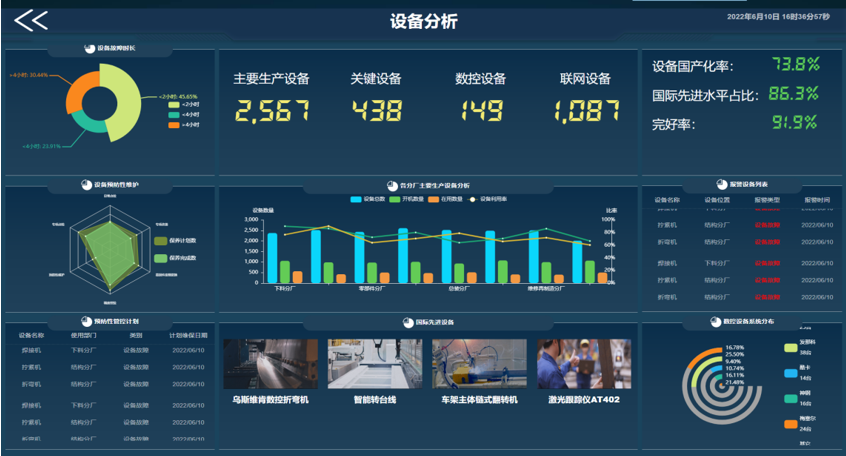
图 设备数据综合分析
计划下达及执行模块:高级计划排程APS系统将计划进行下达到各分厂并集成到MES系统,分厂根据MES中具体订单进行生产的执行。APS系统中生成排程的生产订单、工序计划和设备计划,结合采集的SCADA系统中各设备的实际开完工时间以及MES系统生产订单工序的实际开完工时间,利用finereport对排程计划时间和实际执行时间进行差异分析,获取限制制约生产效率的主要因素。如将APS产能节拍工时和MES执行的生产周期相比较,根据差异进一步优化产品的产能节拍;同时根据排程后帆软FineReport展示的流水线是否连续生产,可对APS系统中的连续批量参数进行设置,如设置为连续批量20台(不同产品设置参数不同),可有效避免像大多数节拍为20分钟产品和节拍为40分钟产品混线所导致的产能浪费问题。
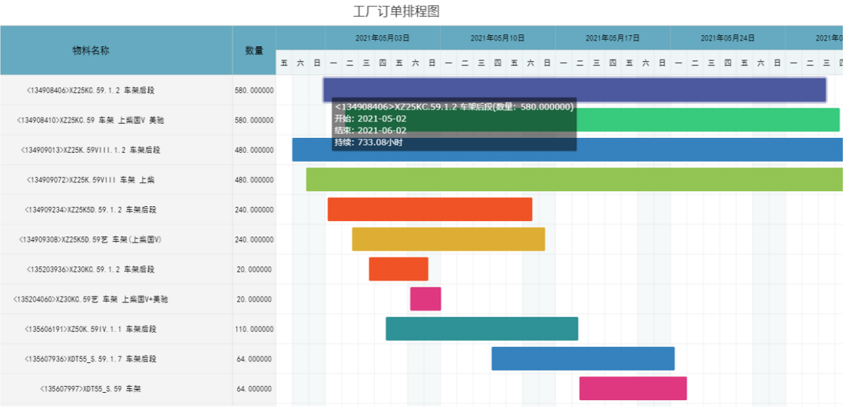
图 APS系统计划排程
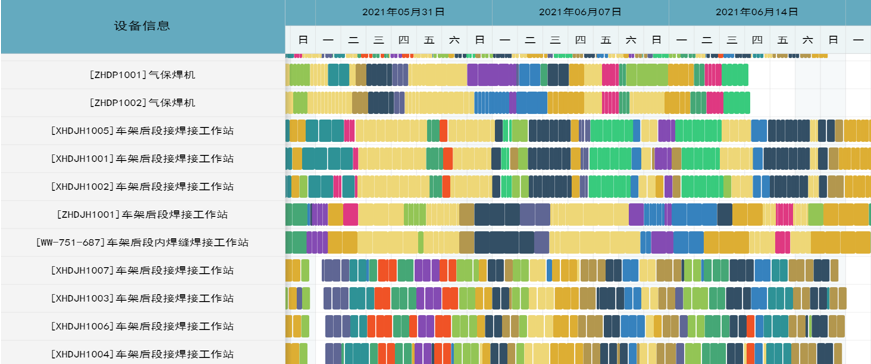
图 APS设备排程甘特图
通过监控APS系统计划、MES及SCADA系统执行等环节数据,可以用帆软报表分析当日计划完成情况、月计划达成率、月计划合格率、批次物料齐套性等指标,如通过物料齐套性,进而分析经常缺料的厂商TOP 10,供应商质量不合格TOP 10等,指导公司供应商采购的调整及质量管控的方向,方便企业提升生产效率、产品质量、精细化管控等能力。
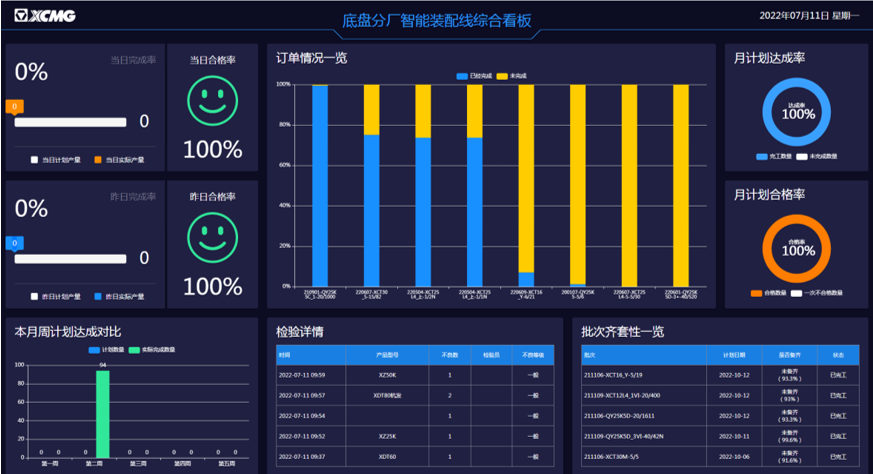
图 生产执行数据分析
成效:通过采用SCADA、APS及MES系统资源动态组织的生产模式,大幅减少了车间计划调度人员进行人工调配资源的工作量,且资源配置更高效,车间计划调度人员减少一半。提升了直产人员工作效率,人均工时日产出提升约10%。在车间智能排产、人机协同作业等其他场景共同作用下,车间关键设备OEE提升了15%,典型产品生产周期提升了50%,一次交验不合格率降低了23%,产品质量的一致性达到了4σ水平。
场景三:五级设备在线运行监测体系
痛点:生产设备的数据采集一直是公司重点关注的问题之一,它是分析生产瓶颈、效率、质量等关键评估指标的重要手段。公司现有的设备种类繁多,接入的数据协议、标准和方式都存在着差异,且老旧设备不满足设备联网的条件,上述各种因素阻碍了设备的大规模互联,各种数据采集也困难重重。
解决方案:公司针对400余台重点设备建立SCADA平台,通过加装智能传感器、运用PLC/DNC/MDC等,实现ModBus、OPC多种协议的设备联网,实现设备运行状态的实时采集、监控。采集SCADA系统的设备参数,依据各分厂功能及设备型号的不同采取纵深到底、精确到设备的模式,利用Finereport搭建工厂级、车间级、产线级、工序级、设备级五套设备分析指标及看板,从效率分析、统计分析、专机分析等多维度、多方位、多视角检测设备状况,保证设备的高效运行,实现设备的精细化管控。
工厂级可视化看板:实现对厂区全貌、车间名及位置、总设备数据、在线设备数等指标信息。
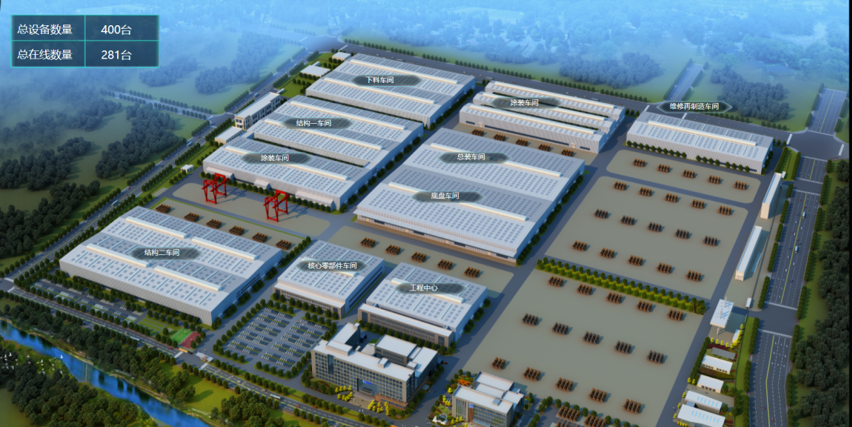
图 工厂级可视化看板
车间级可视化看板:包含车间设备总开机率、利用率、设备运行状态统计、产线产量信息等指标,通过对这些指标的计算,除了分析不同车间当天的开工时长、不同工位上员工工作效率、不同部件平均加工时长外,还可依据历史前7天的车间的总体开机率及利用率,分析车间一周内平均工作效率及同类设备的平均工作时长,多方位分析车间产能及设备效率。

图 车间级可视化看板
产线级可视化:通过对车间产线中各设备轴信息、主轴负荷、主轴倍率、进给倍率、进给速度、主轴转速、程序加工状态、程序文件名、刀具号、报警信息、多轴轴信息、绝对坐标、机床坐标、生产节拍等产线生产信息及产线设备状态、运行状态、告警信息、产线总开机率、利用率等指标的分析,反映产线设备的工作情况,判断产线“忙闲”状态,监控产线设备状态。
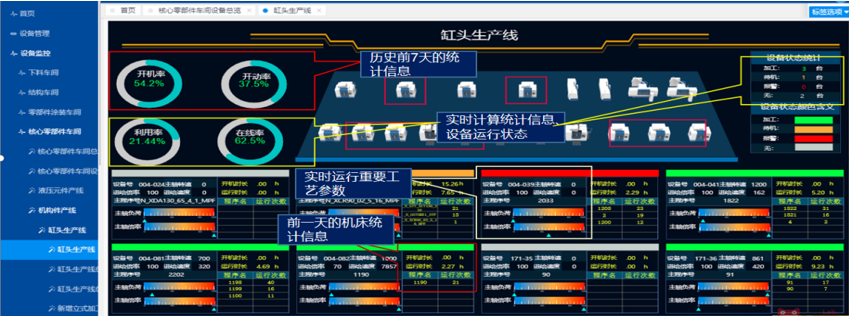
图 产线级可视化看板
设备级可视化看板:针对机加、数控机床、PLC、折弯机器人等不同类别的设备采集设备运行状态、当前报警状态、工艺相关的参数等数据进行设备两率、质量、专机三类分析,用以把控关键设备的使用及利用情况,分析核心参数,辅助研发人员依据设备参数搭建产品的机理模型。
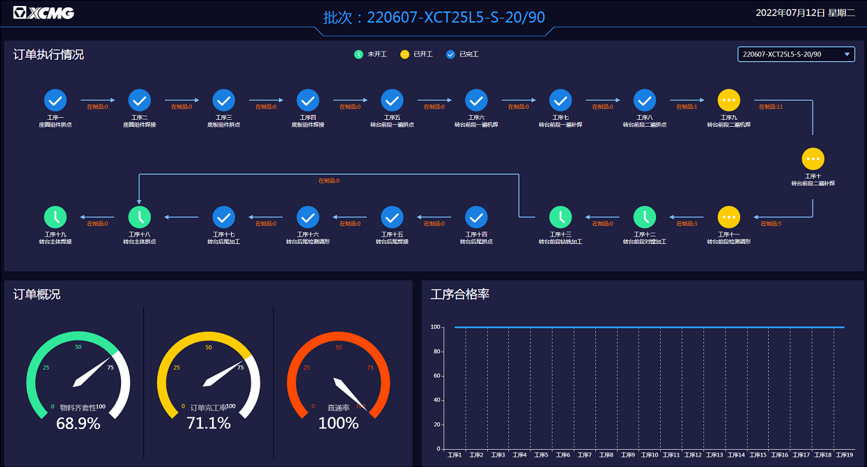
图 工序级设备订单执行分析
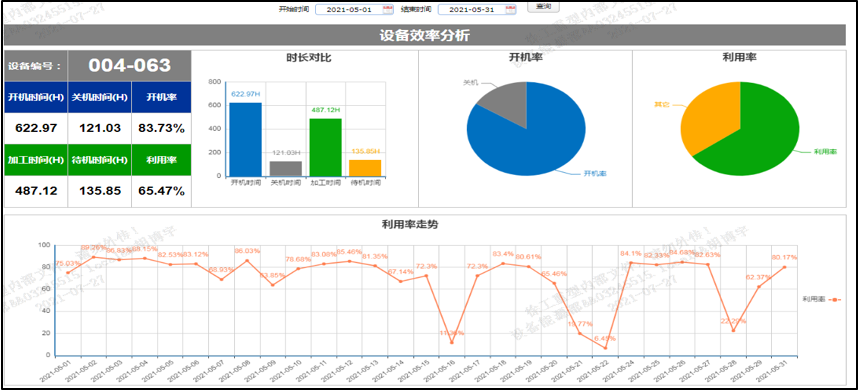
图 设备两率分析
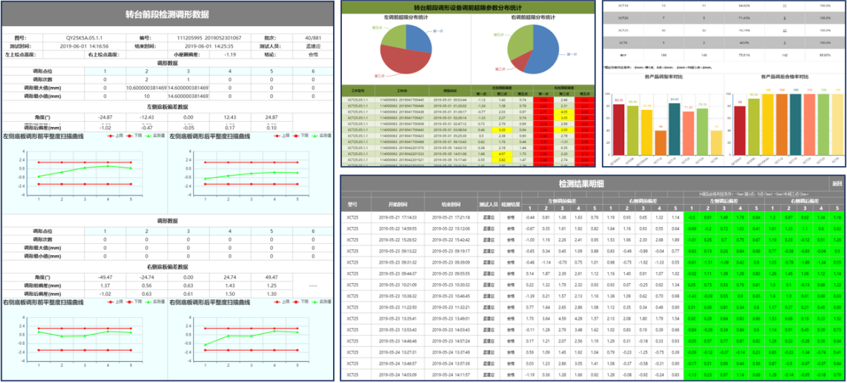
图 专机效率分析
成效:SCADA系统应用后,实现了对400余台重点设备运行状态的实时监控,通过对设备利用效率的统计、分析,统筹管控,公司设备利用效率由36.7%提升至56.1%,效果显著。
场景四:智能排产穿透分析
痛点:依托高级计划排程系统(APS),公司实现了生产的智能排程,解决了无法回复客户交期、订单交付准时率低、交付周期长、资源负荷不清楚、产能瓶颈分析低效、订单交期预估困难、插单管理混乱等突出问题。但APS系统的排程数据难以穿透展示,系统缺乏有效的可视化看板,对生产进度、资源分布及生产瓶颈缺乏有效的展示及分析。因此,在APS系统的基础上通过可视化看板,实现公司级、车间级、工序级生产计划自动排产以及生产过程调度信息的集成透明展示。
解决方案:获取APS系统参数,按照徐工车间计划“周需求、日滚动”的原则,展示不同车间、批次之间的排程计划及资源使用情况。通过帆软可视化看板展示不同产品计划的分布、工作中心班次的分布、当前周计划批次执行的进度、当前各工序在制品的数量、订单各工序执行情况、工序的负载情况、设备的负载情况等,实时透明展现车间生产现状,针对异常问题方便实时调度处理。
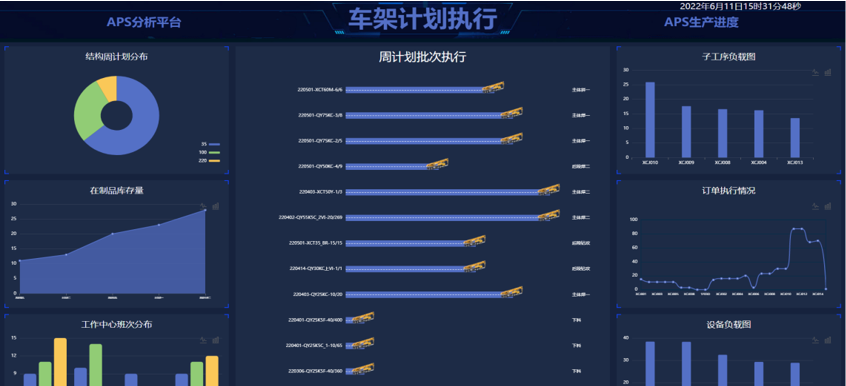
图 周计划排程进度
通过将车间排程人员长期积累的排程规则固化到APS系统中,形成排程参数,并对排程前后的产能进行分析,持续寻找生产瓶颈优化生产过程,对APS中的参数进行调整。例如通过帆软报表展示的生产瓶颈,发现结构上车等待时间比较长,进一步分析发现其中焊接工序及座圈焊工序存在瓶颈问题,通过采取对应手段从而解决该瓶颈。同时根据车间每日生产报工完工数据反馈,实施显示计划执行差异情况,针对异常超期的计划进行实时调度。
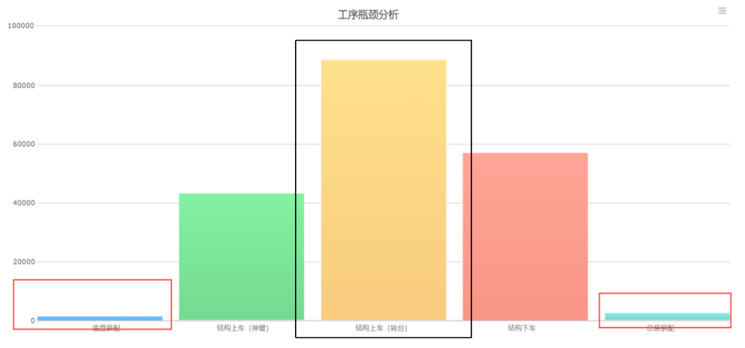
图 生产瓶颈发现
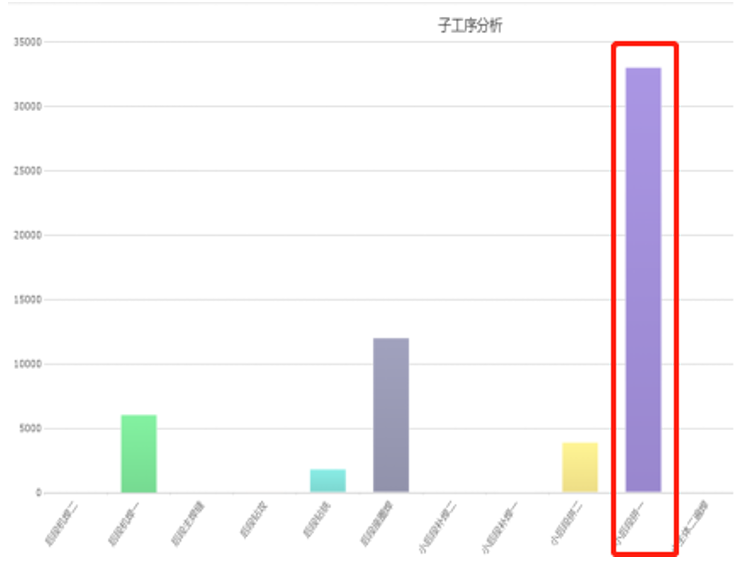
图 工序瓶颈发现
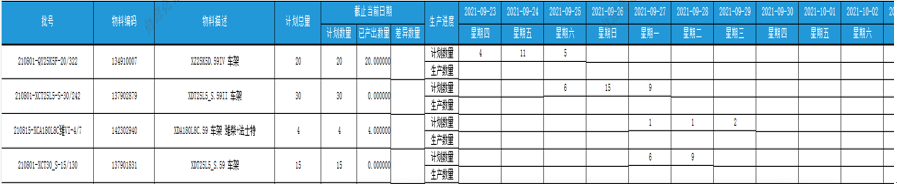
图 日差异报表
成效:APS生产过程数据的透明可视化,可方便展示不同批次车辆的生产进度、资源的占用情况。通过实施,排程人员由每天9*3工时缩短为9*1工时,效率提高300%,客户订单调整和变化由4小时提升到2小时,生产效率提升10%,关键设备OEE提升了15%,同时提高了现场的生产效率,降低了库存,提高了库存周转率,压降在制品成本,实现客户订单的交期承诺,实现对生产排产瓶颈因素的分析和预测。
场景五:直产人员绩效闭环管控
痛点:工厂直产人员绩效考评是工厂人员管理的难点。通常直产人员凭借工时获得绩效,进而获取相应的薪酬。但粗放式的管理模式,经常出现高出勤但工时产出低、高工时但出勤低的异常现象,且绩效数据为敏感数据,基本只公布给个人,再加上员工的出勤情况和工时情况分散在不同核心系统中,如果不把这两个维度的数据拉出来对比分析,很少会有人注意到异常的工时数据,从而无法有效提高员工工作的积极性。
解决方案: 通过MES的工时数据及考勤系统的员工出勤数据对比每个员工的出勤天数及工时产出,同时基于改进的FAST-MCD(最小协方差行列式)人效分析离群点检测算法模型,利用出勤天数及工时数据,对每个分厂直产员工进行聚类,得到“不出力不出工”、“出力不出工”、“出工不出力”三类异常标签,通过分析明确异常人员出勤及工时绩效信息,加强人员岗位及绩效的管控,指导分厂计划调度择优派工。
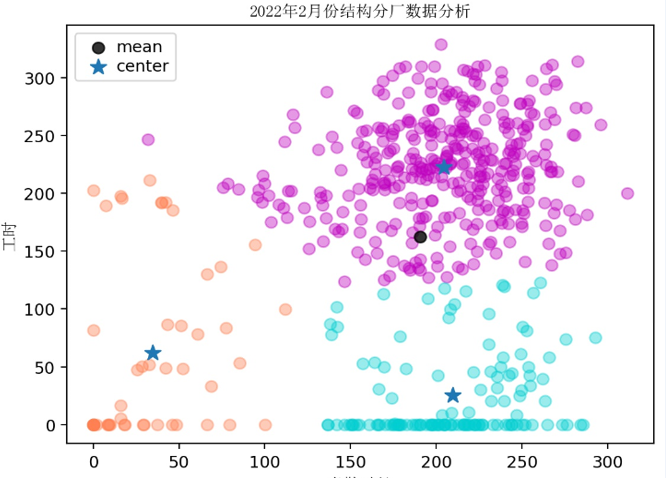
图 结构分厂工时分布图
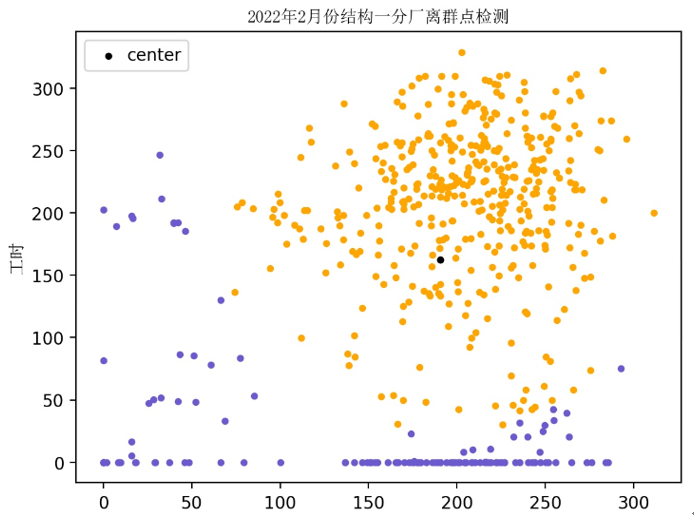
图 结构分厂工时离群点检测分布图
将算法得到的异常的明细数据制作成填报表,在帆软决策平台中设置定时任务,每月15号将异常表明细推送至各分厂劳工员的钉钉端,要求分厂劳工员依据工时及考勤数据核实直产员工数据异常的原因,并将原因回填至明细表中,为后期异常原因分析提供数据支撑。
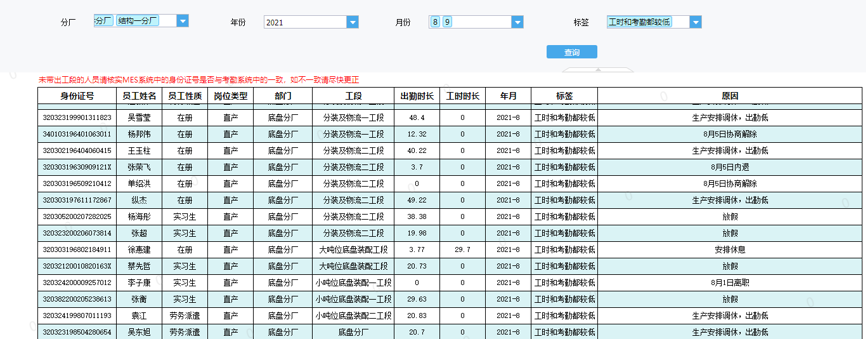
图 异常人员原因收集
对分厂收集到的工时异常员工的原因分类统计,将原因分析结果发布给分厂管理人员,辅助分厂管理人员清晰把握工时异常原因,并根据原因进行管理方式的调整,从而完成直产人员绩效管控的闭环。
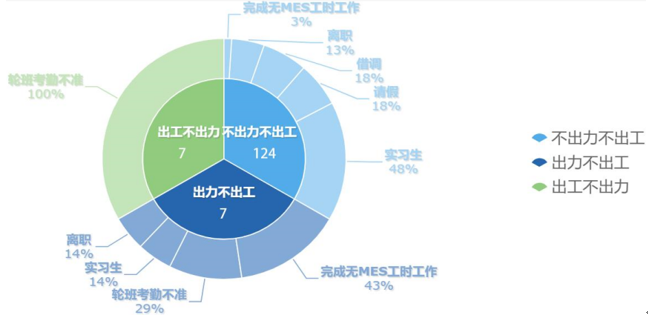
图 人员绩效分布情况
成效:直产人员绩效闭环管控的实施,通过分析考勤、工时数据查找异常原因,并将分析结果反馈与管理人员,打造直产人员绩效管理的闭环,精准定位异常绩效的人员,改变了分厂直产人员的管理模式,完善直产人员绩效的管理环节,加强了人员技能与资质的管理,提升10%的平均绩效评估效率,提高了单位人员平均产出能力。
场景六:营销驾驶舱
痛点:营销驾驶舱主要是为了提升市场部对外部市场的敏感性及对企业在行业内的整体概况,但行业内价值较高的数据只能同通过线下手工统计,其统计数据量大,数据可视程度较差;信息传递时间较长,无法及时得知当前市场波动及目标达成风险,进行销售策略的及时调整和灵活应对;缺少市场历史数据的趋势分析,无法准确的完成对市场预测模型的搭建。
解决方案:联合营销决策平台及CRM系统,对当月企业的销售目标、计划、台量、占有率等指标进行分析,分析不同区域不同职级当前状态下公司的经营现状同时对行业内不同竞争对手在市场上的台量及占有率情况,方便业务人员依据数据进行灵活的变动。
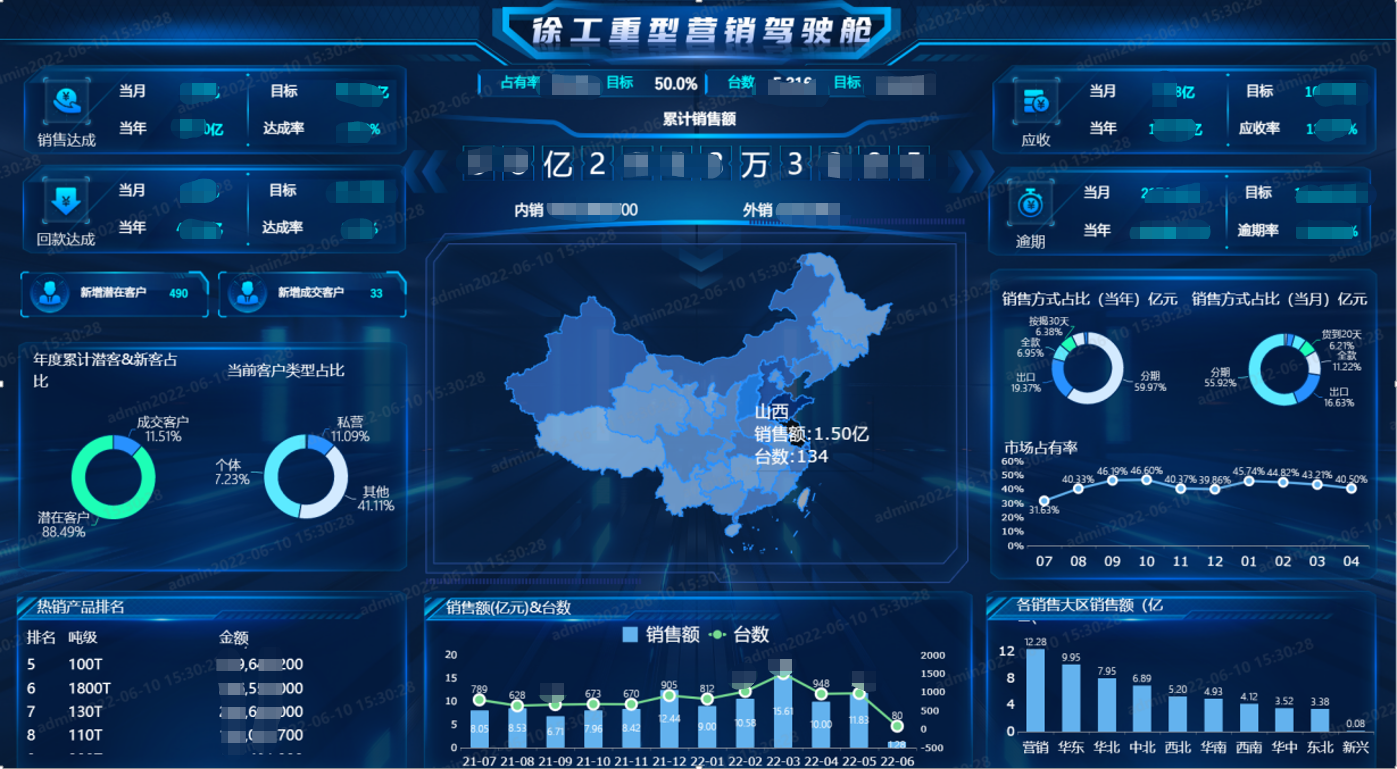
图 徐工重型营销驾驶舱
使用区域台量、车辆开工工时、车辆吨级,车辆占比、实时销量、行业上牌量、行业台量等数据应用大数据、深度学习等技术,结合指数平滑法、决策树、移动平均、灰色关联法等模型,对区域级车辆平均工时进行分析,判断区域对不同吨级车辆的资源需求,从而提升行业需求预测精准度。
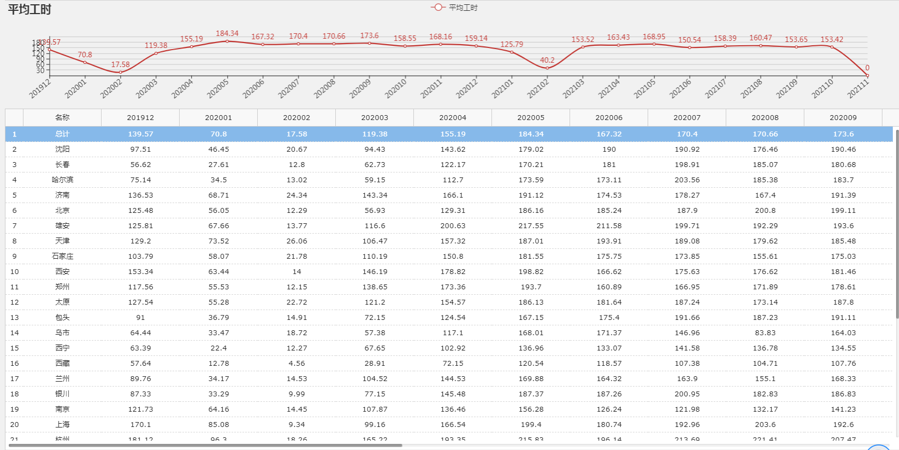
图 市场快速分析预测-区域级平均工时分析
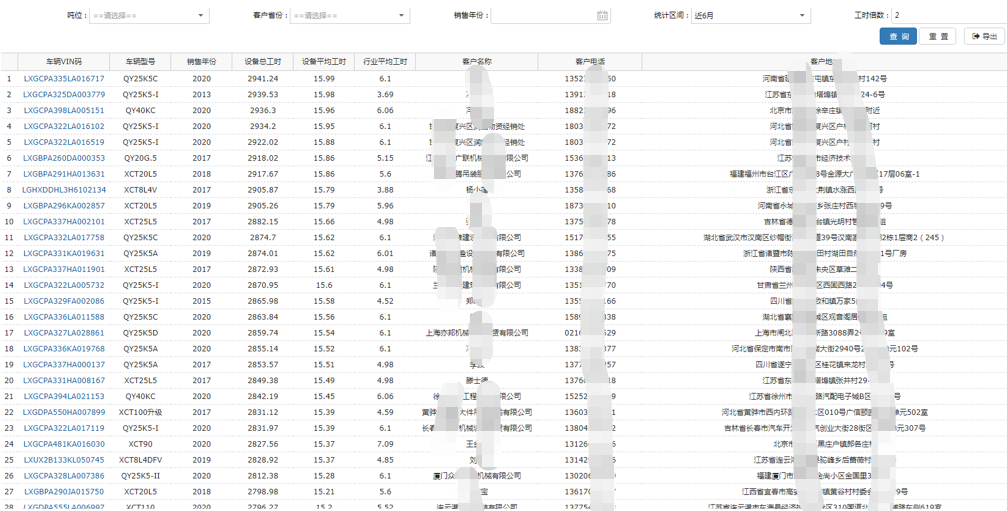
图 市场快速分析预测-单车级经营对比分析分析
成效:营销驾驶舱的搭建,消除了不同职级之间业绩的反复计算与传递工作,提升人员工作效率5%;不同区域内与竞争对手之间占有率、台量的同比环比分析痛点发现时间降低2%,实现了瓶颈问题的快速查找;其行业销量趋势+实时销量趋势+影响因子动态调整的市场预测模型,根据指数平滑法预测未来发展走势,结合内外部环境分析、经济指标走势(GDP、固投、PMI指数等)。近三年来行业销量预测偏差率持续减小,市场预测精准度持续提升。
影响力:营销驾驶舱中市场预测模型的实施对徐工起重机专用GPS车载终端的性能提出了新要求,拉动了车载终端性能的提升,推动了相关供应商的开发能力和制造能力;同时,有效提升了配套采购、市场销售等环节资源匹配的精准性。市场预测模型准确率达到95%左右,已用作企业形成经营决策时的重要依据。
五、项目总结与展望
2021年始,中国迈入了第十四个五年规划,指明了制造型企业数字化转型和智能制造的方向。徐工重型也紧跟国家号召,制定了三步走计划,第一步,开展大数据顶层设计规划,选型大数据技术方案,梳理构建核心业务数据分析指标体系,并同时针对某一领域开展数据仓库建设,开展单一领域的大数据分析;第二步,梳理并完善企业数据资产,开展多维度数据资产治理,开展多领域的业务场景分析,并逐步扩展到企业经营管理层面,为企业决策提供参考;第三步,扩展到企业供应链上下游,通过供应链数据联动,为徐工工程机械形成行业层面的大数据分析平台,并探索试点企业数字资产交易,开展数据资产变现增值服务,将数据真正的资产化,实现企业深度数字化转型和应用。
当前徐工重型已完成第一阶段的建设,构建了数据仓库,大数据分析决策平台,开展了多种时间维度的数据分析。大数据分析决策平台已探索出从数据集成处理到数据分析应用的综合性整体解决方案,考虑到项目实施成本及周期,目前企业内部以点带面开展数据分析场景落地。但由于前期信息化及智能制造建设过程中业务规则的变化及用户使用习惯等问题,大数据分析决策平台与当前业务管理模式还存在一定的磨合期。
大数据不是喊口号,也不是一窝蜂的看着别人上自己也上。上线大数据平台,企业也需要做些转变:
1. 信息化基础要夯实,没有信息化系统,这肯定是不行的,核心业务一定要上系统,通过系统化手段科学进行数据管理;
2. 管理模式上要进行变革。虽然上了系统,但是管理模式还是粗放型的,肯定是不可以的,在上业务系统或者大数据过程中一定要重塑优化业务流程,转变管理模式,否则一切还是老样子,这可能就与上系统的目的背道而驰了;
3. 要遵循循序渐进的规则,切忌贪大求全。业务的成熟度肯定是有偏差的,在实施过程中肯定是先选择较成熟的模块上线,做到由点到线,由线到面,先由典型场景进行突破,可以顶层规划,但是实施要分步实施,先将优势业务借助数字化平台创造出看得见价值,后序才可持续,并最终完成由面到体的体系建设,助力企业探索新的盈利模式,实现企业脱胎换骨的转化。
数字化转型的推进需要企业构建“业务为基、技术为翼、组织为骨、文化为魂”的转型体系,打造“育珠”、“串链”、“结网”的转型方式,逐步演绎,层层推进,徐工重型也在通过自己的方式,实现企业数字化转型的落地,发展新业态、新模式。 |