发现问题:过程不良是指生产过程中发现的来料缺陷产品、过程加工的废品、返工返修产品及偏差使用产品,该类产品的产生,基本不能正常使用,造成生产成本的浪费。在学习和掌握数据分析之前,桥二厂内部分析的过程为:从ERP系统导出当期产生废品明细,通过人工对数据进行整理、规范、汇总,编制周期性废品分析报告,每次历时3-4H。数据的不及时性和人工整理工作量的庞杂性是制约效率提升的核心因素。
解决过程:首先,将桥二厂过程不良明细进行分类,同时以2021年1-9月份过程不良数据为基础,开展报表设计及数据分析,通过分析,发现:
①桥二厂2021年过程不良仍包含料废、工废、返工返修和偏差使用4个方面;
②其中,料废共涉及xx个供应商、xx件废品数量,涉及金额xx元;工废共涉及xx件废品数量,金额xx元;而返工返修和偏差使用仅涉及少部分产品;
③为持续降低生产过程成本,提升分厂过程质量稳定性,我们从供应商料废集中点及工废制造原因两方面进行详细分析,寻求改善点。
其次,报表分析思路主要从两个维度展开,第一部分针对料废,我们的分析思路是,以废品金额为前提,通过层层钻取,聚焦主要厂家、关键产品、重点缺陷位置,以此实现精准改进。
通过帕累托图、气泡图对料废金额、数量进行分析,锁定重点产生料废供应商厂家,再通过数据联动、由柱形图、玫瑰图、词云图等层层钻取,实现关键产品和重点缺陷位置的聚焦,以期为供应商提供改进方向。
通过分析,得出建议:①xx公司针对减速器壳轴承孔壁薄、大面料亏、HD标识处漏气进行重点改善;②xx对于250桥壳桥管安装孔内砂眼进行专项整改。
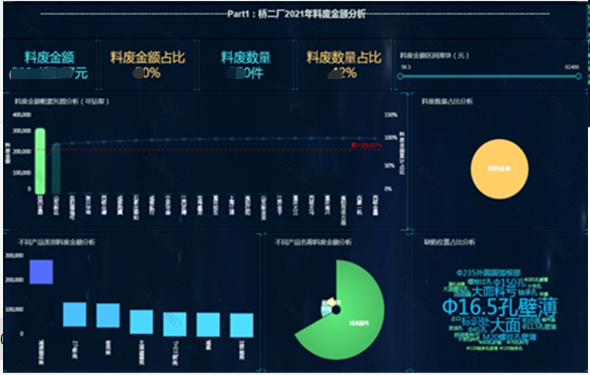
图1:桥二厂2021年料废金额分析—原始状态
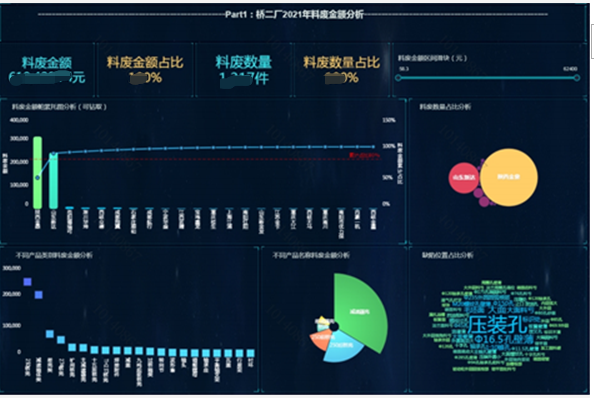
图2:桥二厂2021年料废金额分析—钻取状态
第二部分针对工废,我们以致废原因为前提,从工废数量上进行分析。通过对工废数量的层层钻取,锁定导致产品致废的主要原因,进而制定针对性的改进计划。
通过帕累托图,对工废致废原因进行分析,锁定关键致废原因,再通过数据联动,由矩形树图、词云图、条形图等层层钻取,得出根本致废原因。
通过分析,得出建议:分厂内部应结合微课、OPL等点对点培训,重点提升员工数控类设备刀补调整和首件对刀技能,规范刀具寿命管理。
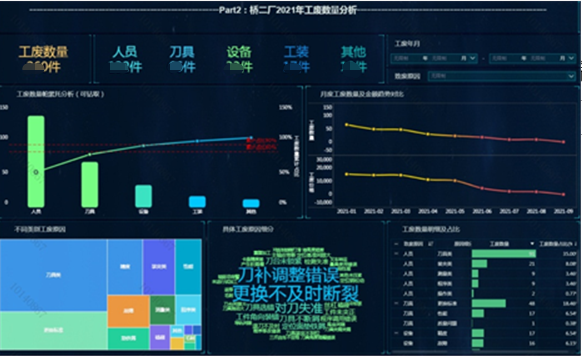
图3:桥二厂2021年工废金额分析—原始状态
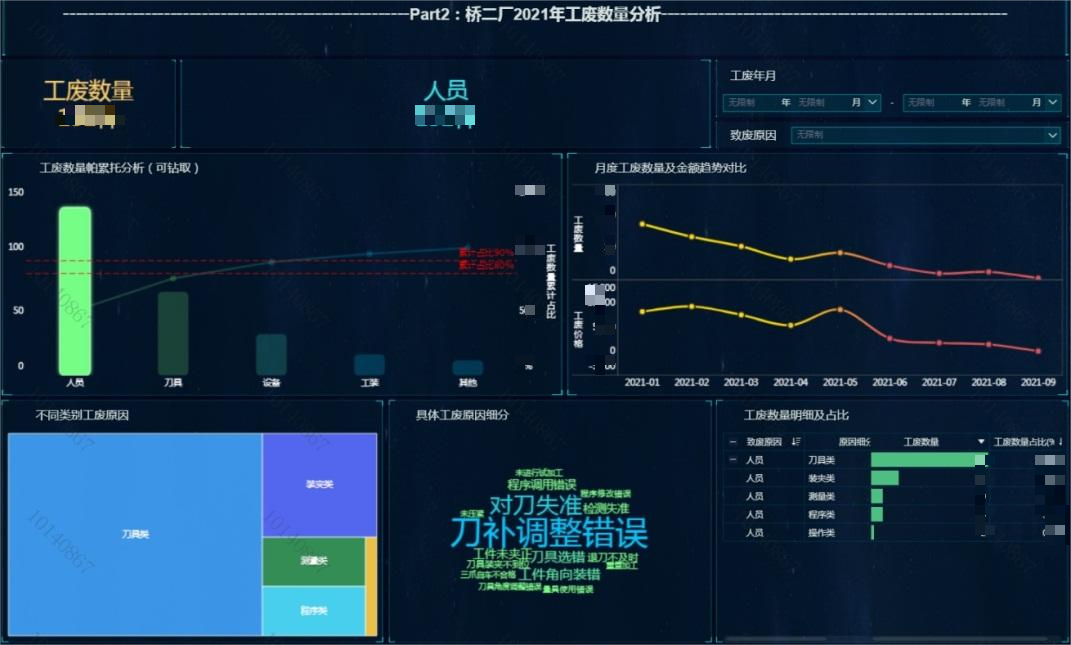
图4:桥二厂2021年工废金额分析—钻取状态
第三部分是桥二厂1-9月份料废及工废的明细展示,明细可便于管理者查看、导出使用。
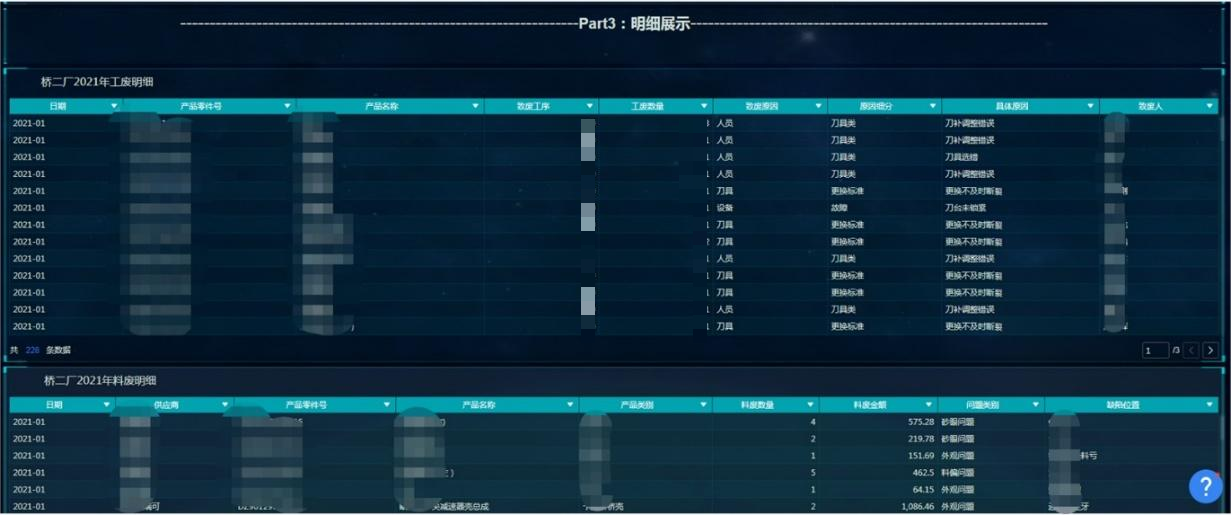
图5:桥二厂2021年工废、料废明细
场景价值:大数据平台与BI工具的运用显著提升了效率,由原来的数据整理、报告生成需要1天时间,缩短至1小时内完成,效率提升了80%,同时能够方便的实现数据报表的一键分享。在精益六西格玛驱动下,桥二厂借助分析洞察,成功识别并实施改进项目,包括1个黑带和2个绿带项目,优化了供应商技术对接,有效降低了废品生产率5%,为各分厂每年节约成本约10万元,有效促进了生产产品及生产质量的提升。
|