*本文为2022中国数据生产力大赛银奖案例,未经授权禁止转载!
南京东华智能转向系统有限公司始建于1958年,自1970年开始致力于汽车转向系统及其零部件的开发、制造、销售和服务。公司隶属于上汽集团,为国家高新技术企业、全国汽车标准化转向系统分技术委员会秘书长单位。
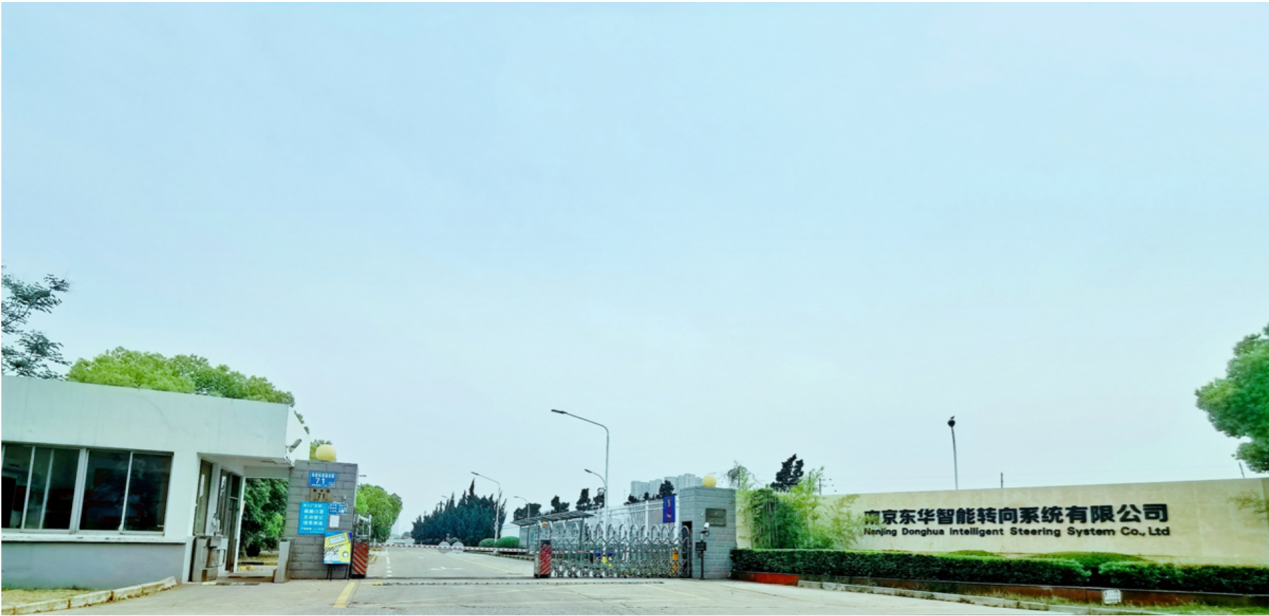
公司产品主要针对国内自主品牌乘用车、电动车市场。其主要客户为上汽通用五菱、上汽荣威、MG、MAXUS、北汽新能源、奇瑞、比亚迪等汽车厂商,具备年产140万台(套)电动助力转向系统的生产能力。
公司现为江苏省星级上云企业,目前正着力推进的数字化智能工厂项目涵盖生产计划、车间执行、采购物流、仓储管理、供应链协同、质量管理、设备管理、新品变更管理8大业务模块,围绕精准生产与动态决策两大转变,数字化推动持续优化与效能提升,助力企业卓越运营。
质量问题贯穿于产品整个生命周期,与公司各部门业务都密切相关,根据业务需求,公司现有ERP,MES,PLM,EICP等系统,各业务流程数据存储在各种不同的数据库,SQL sever,MYsql等,数据整合汇总比较困难,不便于质量信息的关联分析,通过FineReport强大的自定义数据连接功能,打破了各系统之间的信息孤岛,将产品整个生命周期的数据以电子报表的形式呈现在FineReport平台上,结束了从前纸质报表的时代。
公司系统-数据交互框架图
价值二:
通过FineReport数据决策平台建立了公司分部门分层级KPI指标多维度报表(时间维度,产线维度,供应商维度,客户维度等),实现了采购、物流、生产及客户等产品全生命周期质量数据的实时监控与相互串联,及时掌握产品各阶段质量问题的预警及产生,实现问题源快速锁定与紧急遏制,节约了定期数据汇总分析的繁琐操作。
质量层级报表实时监控
价值三:
运用OKR思想,结合企业目标制定量化关键结果目标阈值;运用PDCA法则,建立目标达成促进体系,闭环管理产品生命周期内各个阶段质量KPI指标,实现质量成本降低20%。
痛点:
1、缺少对供应商的执行过程管理监督
企业跟供应商合作是一个长期而持久的过程,对于合作过程中订单的发货管理、订单的执行、原材料的价格波动以及合同的进程监控保证有很高的要求,目前这些信息不透明导致供应管理黑匣。
2、产品出现问题没办法精准定位到供应商处
当产品出现质量问题时很难直接定位到相应的供应商,无法快速对供应商提供的原材料的质量进行追溯分析,整个过程耗费大量人力和时间资源。
3、供应商绩效评估和淘汰机制薄弱
企业通常采购完成后,缺少系统性的对供应商相关数据指标的考核和淘汰机制,数据信息不流通不透明,整个供应商管理流程没有形成闭环,容易产生劣质供应商问题。
解决过程:
-
1. 供应链质量看板
采购件质量问题是采购供应链中关注的重点,根据评价指标搭建分析看板,分别从零件PPM、供应商零件质量抱怨、车间停线次数以及供应商质量绩效红黑榜四个维度对供应链质量问题进行展示。采购工程师根据供应商绩效红黑榜以及供应商零件质量抱怨对供应商进行积分惩罚,并对良好质量供应商进行激励。
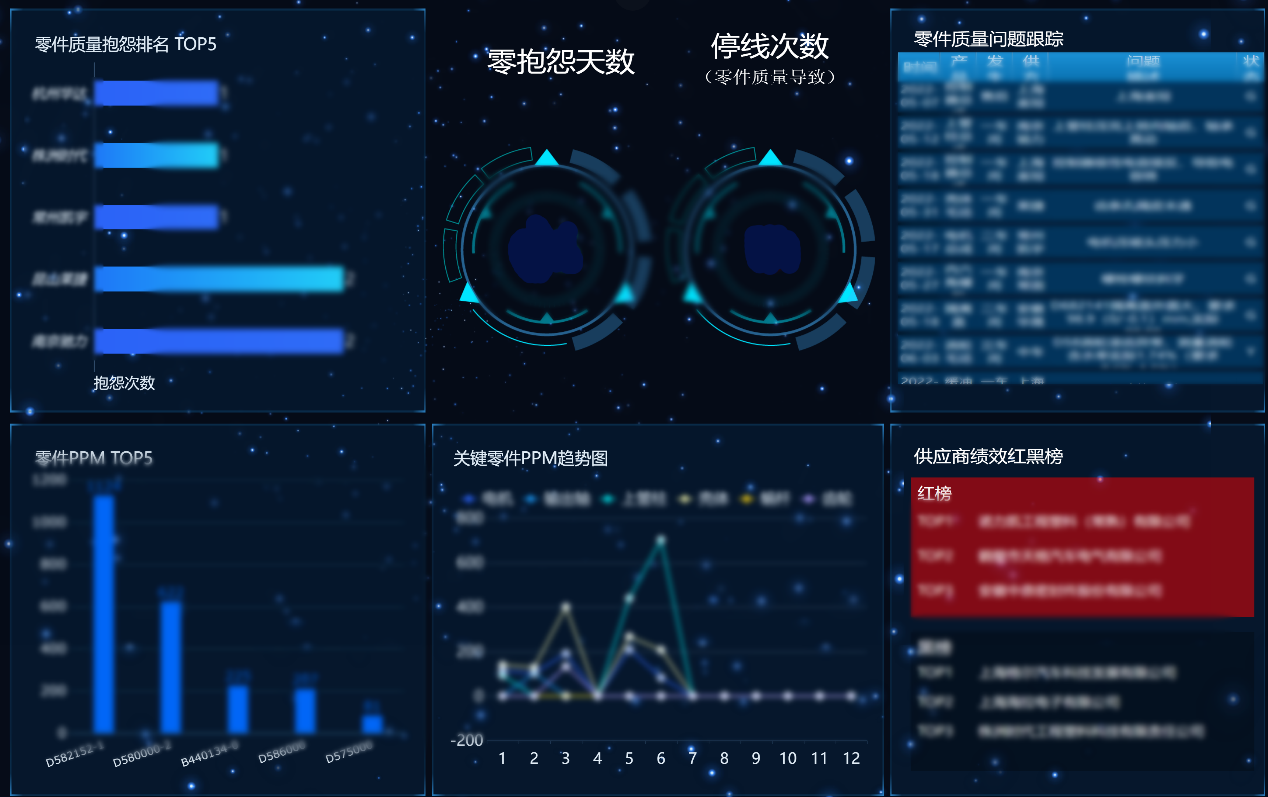
采购质量大屏
对于采购到件,根据到货产品的一次合格情况对产品进行检验,数据来源包含了来料检验和收货异常问题,从年度、月度、供应商三个维度对采购零件合格率的统计情况。
后续针对采购件产生的问题,采购质量工程师制作工单并反馈到供应商端,对问题关闭情况进行跟踪,对未关闭问题进行跟催,形成供应商质量问题治理闭环。
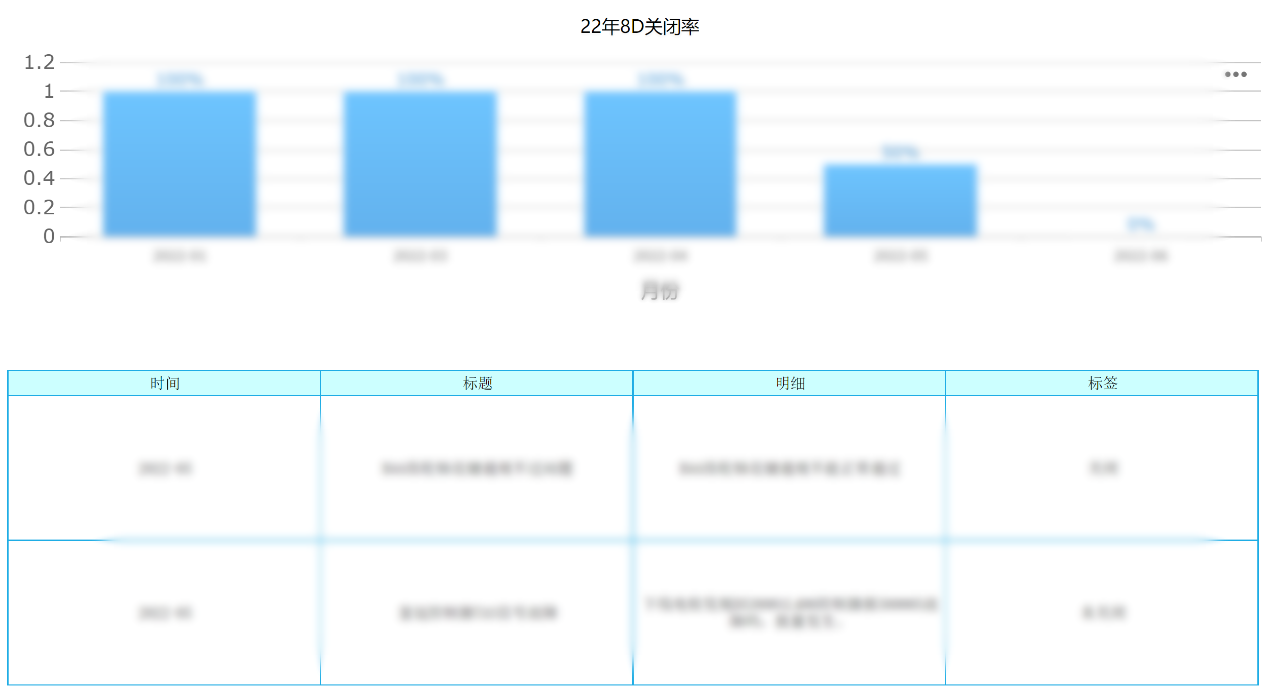
供应商问题关闭情况
为保证供应商中生产工具(模具、刀具等)的质量,通过统计供应商到货数量计算模具寿命并设定预警界限。当模具寿命超出预警界限,通过钉钉集成将预警信息自动发送到采购质量工程师,采购质量工程师对该部分模具收严管控,增加质量检验频次。通过模具寿命和质量检验数据的积累,不断优化生产工具使用寿命。
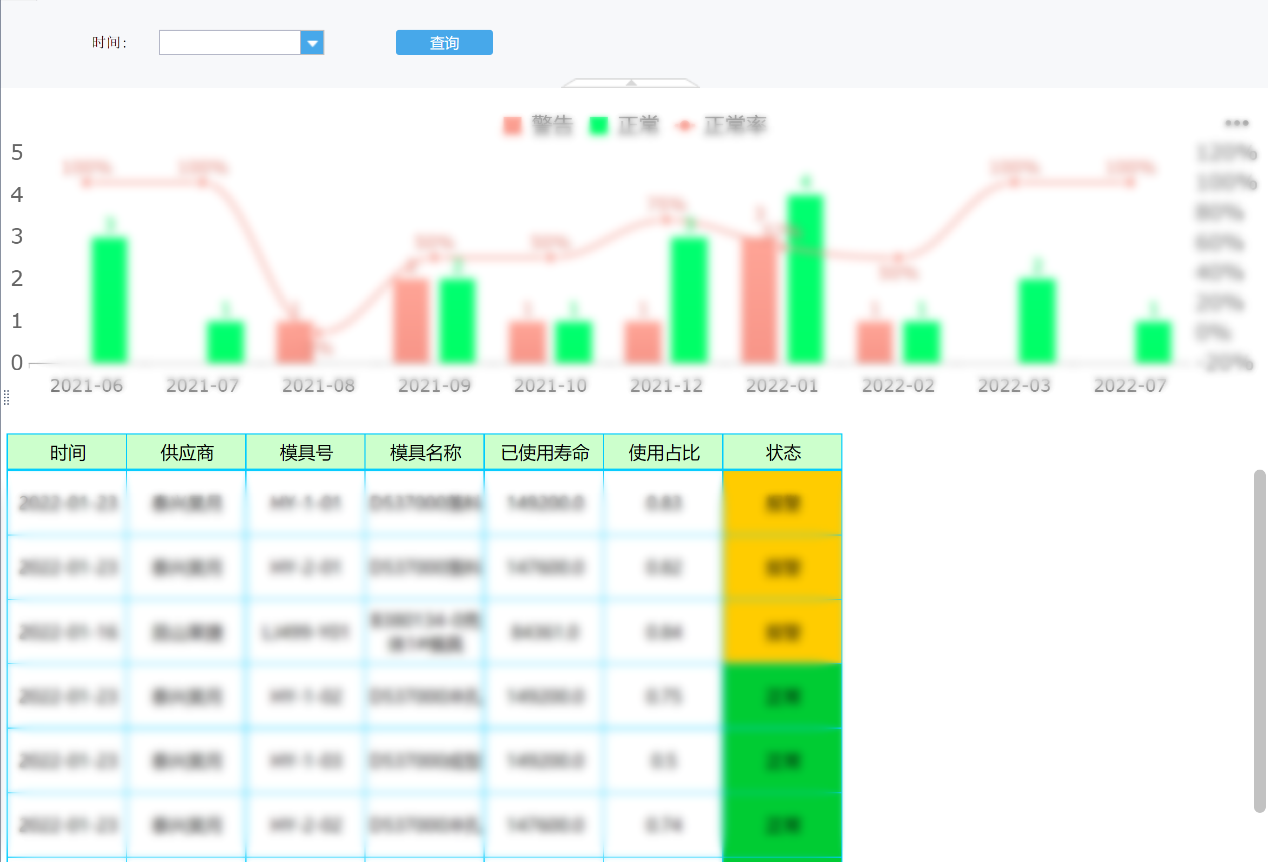
模具使用频次
2、采购订单交付
根据生产需求,采购部门制定采购订单下发到供应商端,供应商根据采购订单进行备货,并对供应商的物流进行跟踪。通过采购监控大屏实时展示当前的采购订单进度,便于业务人员了解物流进程。从年度交付准确率、月度准确率构成以及月度准确率交付趋势等,实时展示当月订单物流交付情况,并对订单进行分析,推动业务人员优化供应商物流逻辑,促进供应商交付准确率提升。
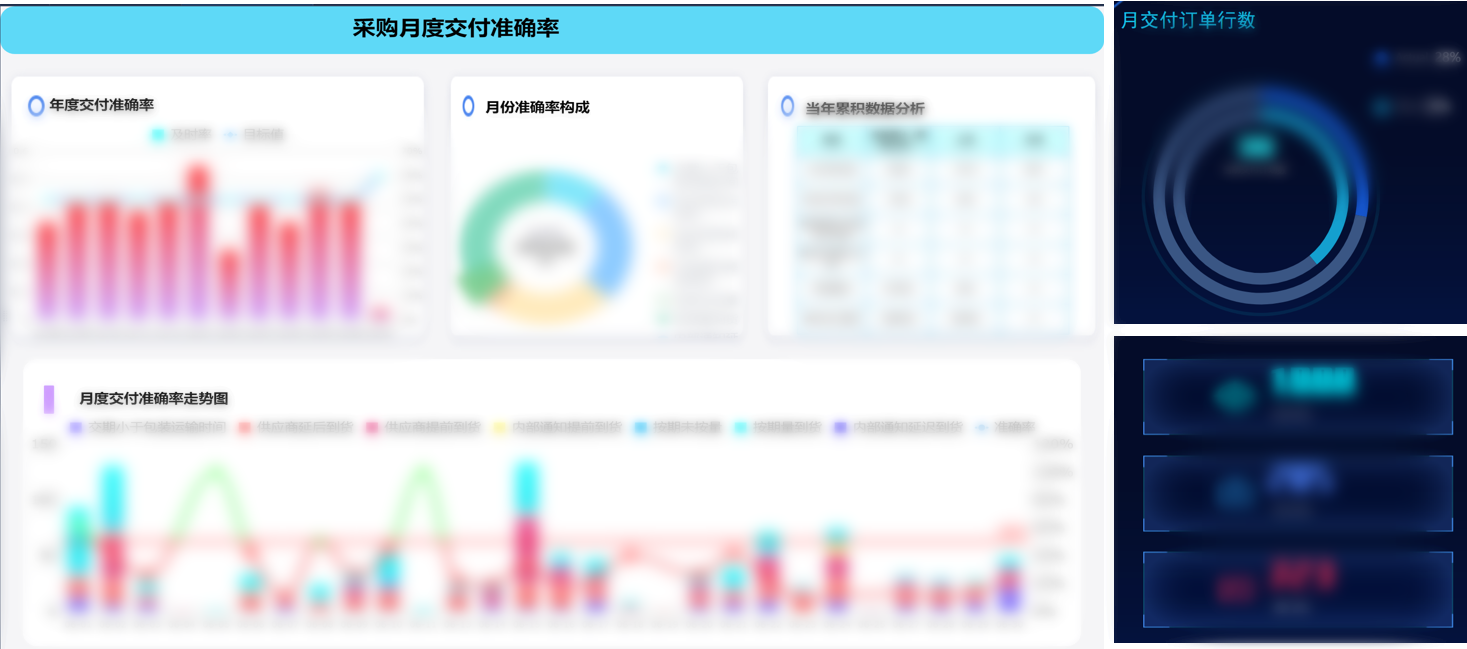
采购月度交付准确率
价值:
1、打破了以往对供应商在执行合约提供服务过程中的信息黑匣,优化整个执行过程的流程管理,在供应商执行的过程中能够有效进行监控和及时对采购方进行预警,保证双方合作的长期稳定。
2、将产品的相关信息跟供应商提供的原材料单号进行匹配,对客户投诉的产品问题进行质量追溯,精准对应到相关的问题供应商,节省了人力手工匹配的精力和调度时间,方便采购方进行问责记录。
3、通过供应商质量问题频率以及供应商物流响应程度两方面,对供应商提供服务的结果进行打分排名,及时对供应商进行淘汰和引新,保证企业优质的供应链管理系统。
痛点:
1、工程师不能实时监控产线良品率并作出响应。
2、生产数据不能一站式查阅,制约工程师关闭问题速度。
3、过程质量预控,人工统计仍为主要手段。准确性和实时性得不到保证,无法有效起到预警作用。
解决过程:
1、产线运行状态监控大屏
以产线为单位:①监控开班首检、过程巡检的完成情况;②监控工序一次合格率和产线直通率的达标情况;③监控班产完成情况和SPC报警情况。④统计产线缺陷并排序,展示TOP5问题。当出现红色时,工程师收到短信通知并作出响应,有效提高响应速度。重点分析解决TOP5,抓大放小,有限精力解决更多的问题。
2、产品关键特性管制图
实时获取加工结果并更新管制图,触发(黄色)预警和(红色)报警,信息通知工程师处置。工程师根据历史数据,优化加工参数,可实时得到验证数据,对比优化效果,提升措施有效性。
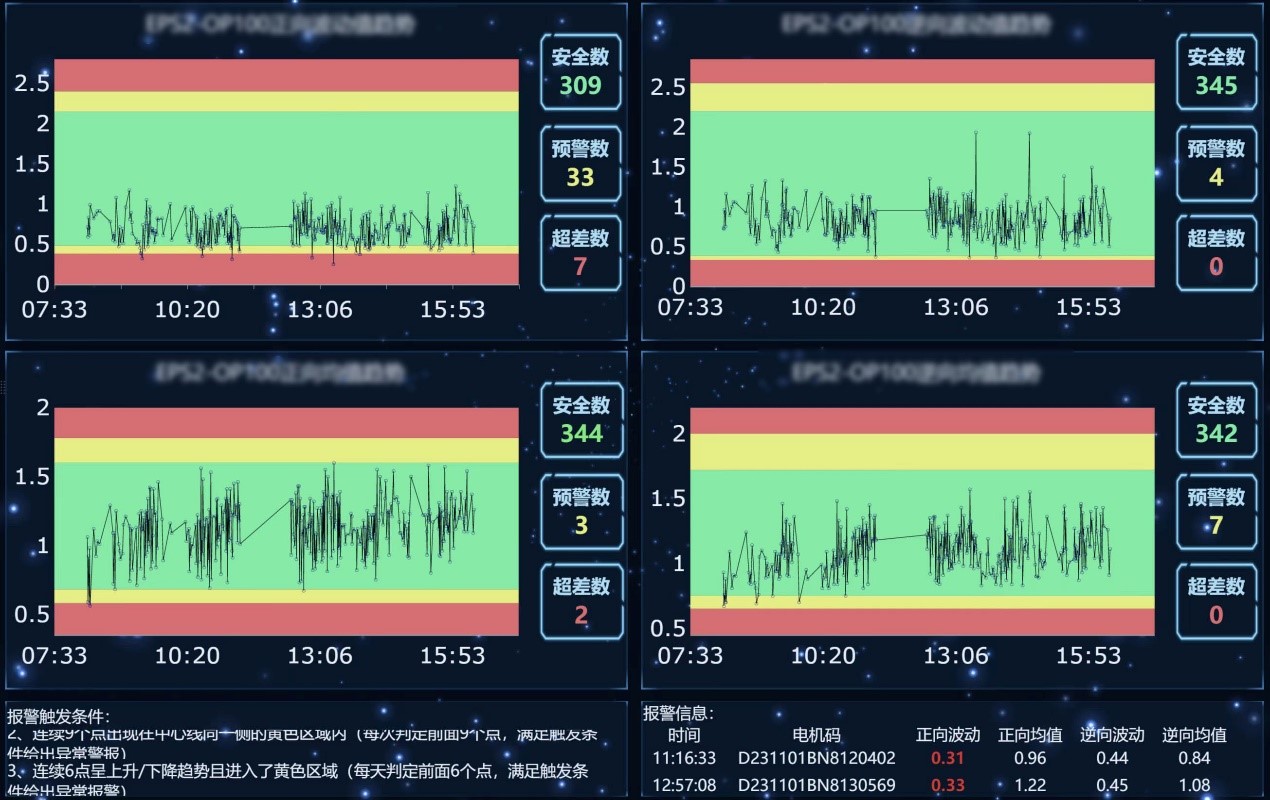
关键特性管制图
3、SPC管控图预警
实时监控工序关键尺寸加工稳定性,出现异常报警,信息通知工程师处理。工程师可分析历史数据,制定工序能力提升方案并实时观察措施效果。
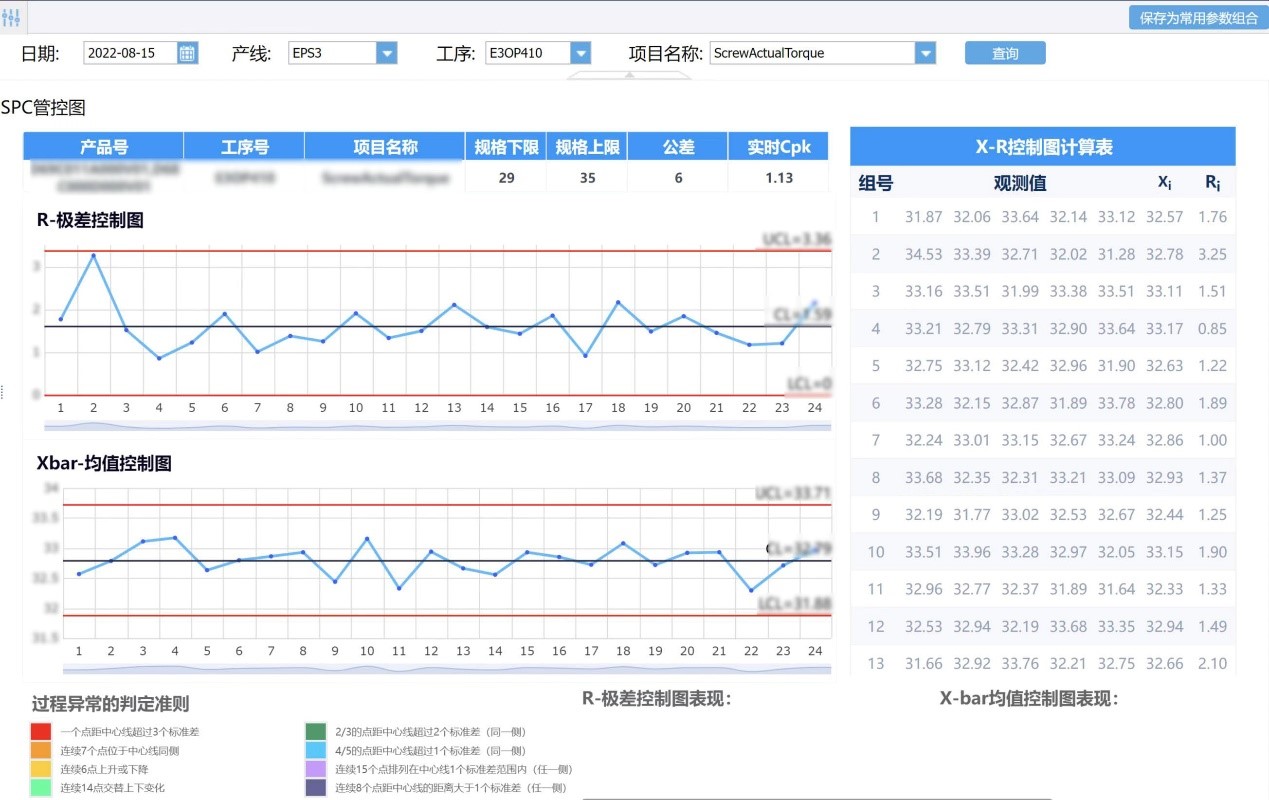
SPC管控图
价值:
预警、报警由人工转由系统执行,提高了效率和准确率;现场问题的处理,由主观经验判断变为数据支撑结论;已处置问题,通过实时数据展示快速的关闭;过程能力提升的数据依据更准确,支撑数据更易获取,提升效果更易确认。
近年来,制造企业越来越重视管理,逐步改善车间的生产条件,为MES系统的实施提供了良好的车间环境,也便捷了质量信息的追溯。帆软的数据分析填报功能比想象中还强大,要做好规划充分利用,快速开发适合本公司特性的相关系统项目,引入低代码平台,入手快,投入少,符合公司对未来规划的发展趋势。但是帆软终究只是一个工具,最重要的还是需要公司从实际出发,做好规划调研报告,才能有效地帮助管理人员加强管理和控制,保证信息处理的及时性,通过流程重组,合理分工和明确职责,达到精细管理的目的,并增强企业竞争力。
注:为了便于阅读,本文对材料内容做了删改,感兴趣的朋友可以点击阅读原文查看原帖。
|