2024年9月24日,第三届“鼎新杯”数字化转型应用优秀案例评选颁奖典礼在北京落下帷幕。
本届鼎新杯以“数腾劲浪、鼎新引领”为主题,共设置了25个方向,经历了案例征集、全国入围初评、人气案例评选、全国终评,历时5个月。在案例征集期,大赛共收到来自全国31个省、自治区、直辖市的1000余家企业、科研院所、行业协会、政府机构等单位的近4000个申报案例。
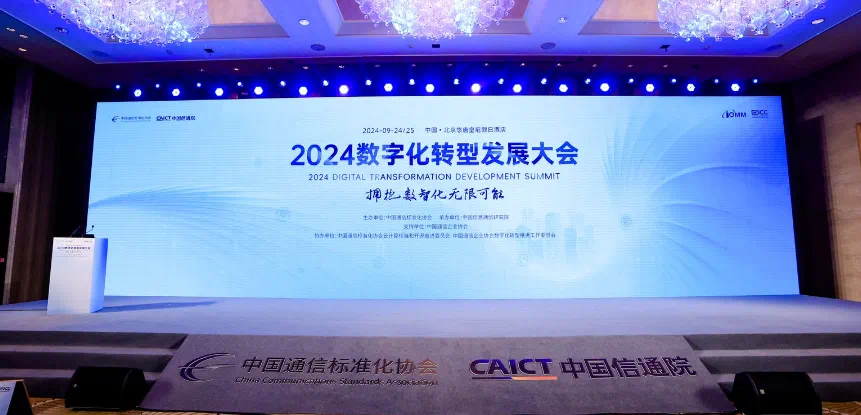
重庆长安汽车股份有限公司两江工厂凭借《量产工厂的数字化转型》从案例中脱颖而出,荣获本届大赛一等奖!
重庆长安汽车股份有限公司,是中国汽车四大集团阵营企业之一。为实现向智能低碳出行科技公司的转型目标,长安汽车迈出了第三次创新创业的步伐。其核心聚焦于“实现高效、柔性、敏捷制造,快速满足客户大批量个性化定制需求”,以制造技术和制造管理为双翼,通过模式创新、技术创新、智能赋能以及管理升级,将制造能力打造成为公司的核心竞争力,以此推动公司的创新创业计划迈向成功。
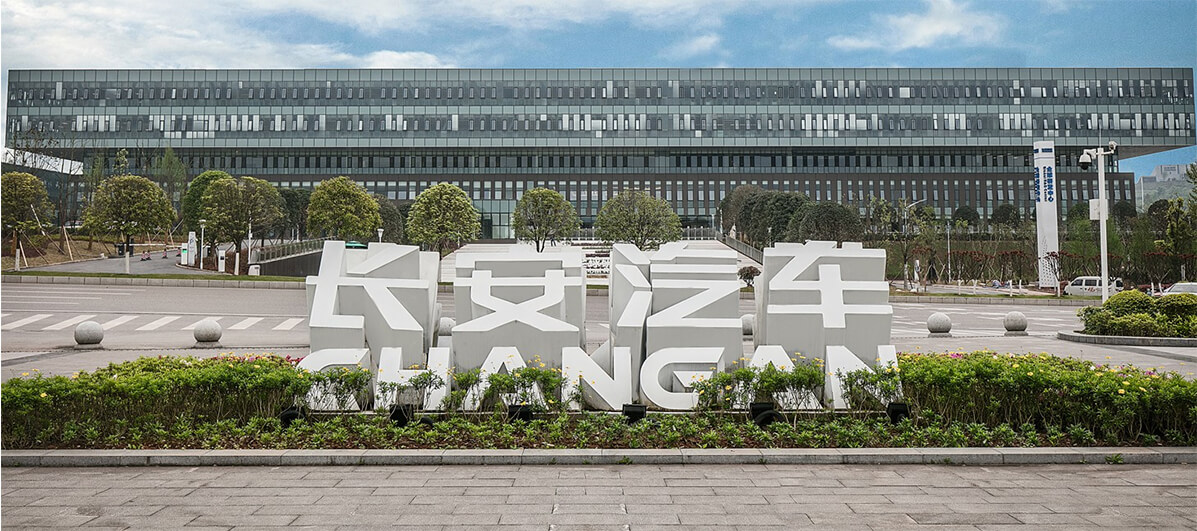 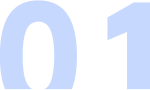
复合型人才成为数字化
转型升级的迫切需求
两江工厂作为长安汽车生产的重要基地,信息化建设对其发展至关重要。不过随着两江工厂数字化转型的开展,个性化需求增多,传统工作模式低效,数据口径偏差等各类挑战接踵而来,特别是对于人员素质方面,不仅需要在制造流程和技术上实现创新,更需要对人才结构和能力提出全新的要求。
因此,培养具备数字化素养和技能的人才,已成为两江工厂数字化转型升级的迫切需求。
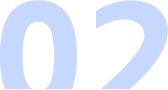
全民开发,提质增效新模式
“只有通过加强数字化人才的培养和引进,才能够更好地适应数字化转型的步伐,推动公司向智能低碳出行科技公司的转型目标稳步前进。”两江工厂智能制造主管魏泽淇介绍,两江工厂通过整体牵头的形式,从各部门单位抽调2-3名员工作为种子选手,参与每年一次为期2个月的工厂级零代码培训,让这些种子选手深度掌握数字化技术的同时,兼顾负责本部门整体业务系统搭建及本部门其余人员培养。
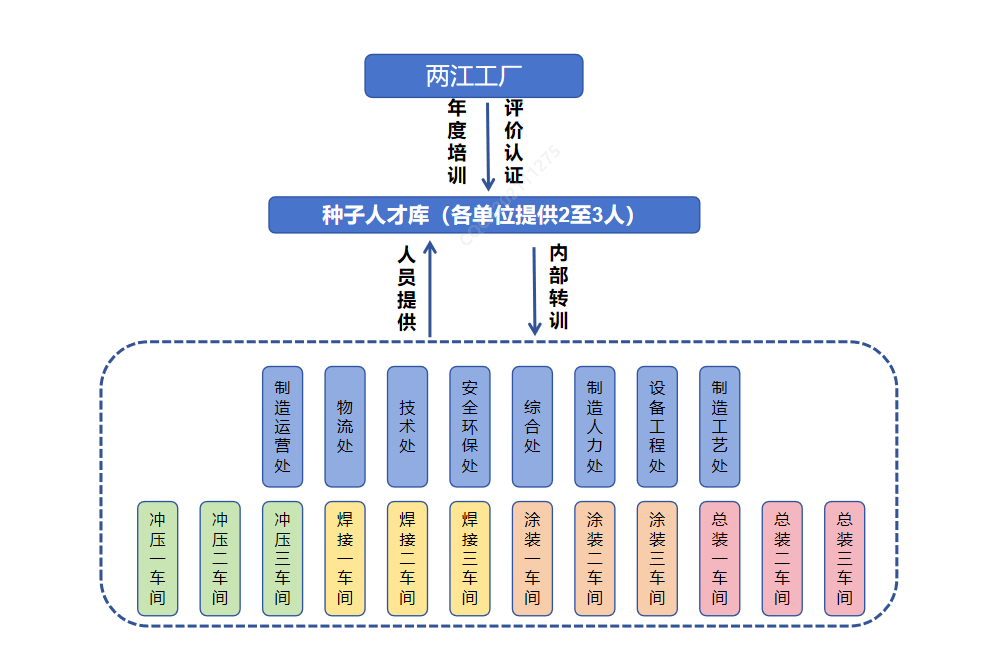
经过简道云团队近一年的零代码赋能培训,两江工厂员工的零代码开发能力得到了大幅提升,零代码基础开发能力实现了全员覆盖,一线部门累计自主开发业务应用超过50个。此外各职能部门及生产车间均通过简道云零代码平台搭建了本部门业务管理驾驶舱,实现了本部门90%CPS业务的E化替代,总体日均使用人数1300+,日均操作量8000+,办公效率提升近50%。
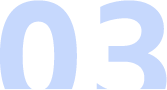
质量是造车的立身之本
质量作为造车的底线,是车企的立身之本。在两江工厂一线业务员工自主搭建的50余个应用中,各项质量相关的流程及程序占据了大多数,返修管理、错漏装闭环管理等程序的普遍应用,大幅降低了质量产品流出工厂的风险,同时也提高了两江工厂各部门的质量排查返修效率。
之前两江工厂出现因备件库存管理不当,且遇到紧急需求时,零件不够用的情况,只能临时寻求兄弟单位借用。魏泽淇介绍,如今来自设备部门的同事通过简道自主云设计了对备件库存进行系统化管理的应用。
通过设计简道云备件管理流程,就可以实时对备件库存进行监控,当库存低于安全值时自动发起采购,并传递给管理负责人进行审批,有效避免了库存不足导致的效率损失。
同时设备管理业务部门还设计了备件管理驾驶舱,整个备件管理过程基本实现自动化,员工仅需发起领用流程及审批采购申请,无需对备件余量进行监控。“驾驶舱的加入为备件的精细化管理提供了数据支持,也帮助了员工对备件管理的理解深度,并直观的掌握备件状态,减少了廉洁风险。”
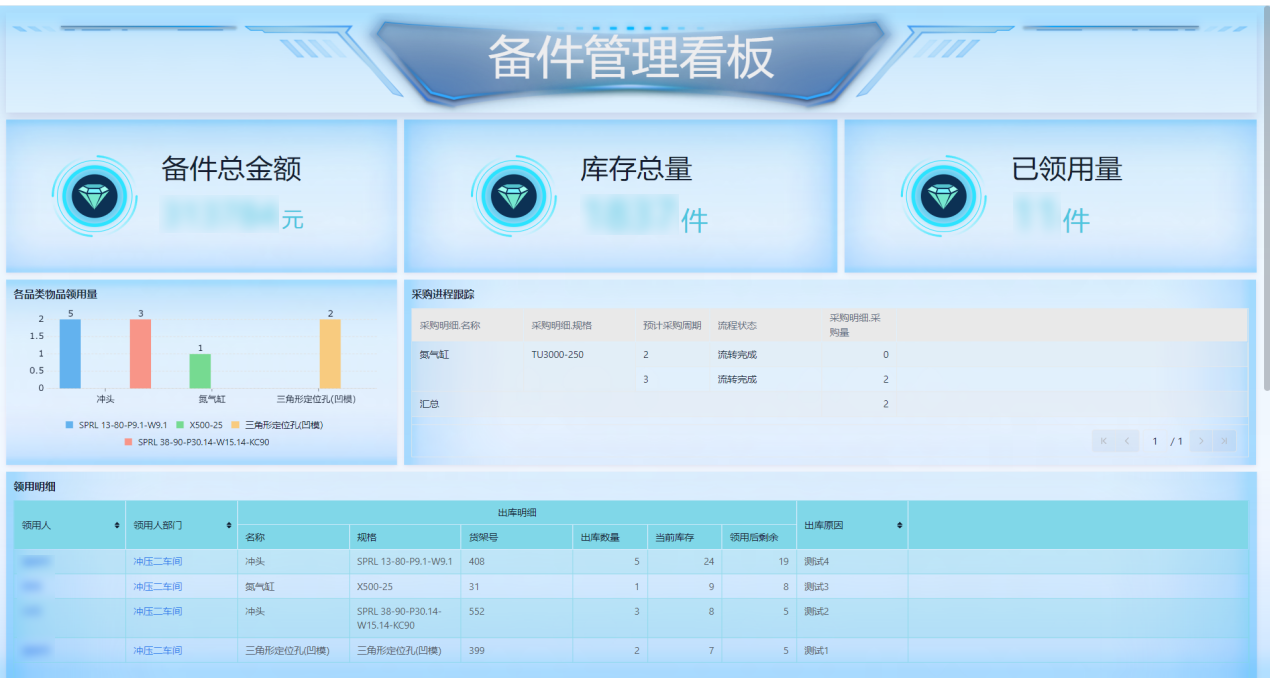 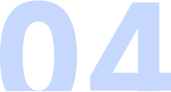
以精益之心打造极致产品
在汽车制造领域,如何正确识别色差对于确保产品质量以及维持良好的外观至关重要。它不仅能够保证汽车整体外观的一致性和协调性,提升车辆的美观度和档次感。还可能影响消费者对汽车品牌的信任和满意度。
作为行业内的痛点问题,之前两江工厂也会遇到外饰件与车身在各自色差检验阶段均合格,但是整车装配后车身与外饰件目视色差明显的情况。此外色差数据检测和记录方式仅能确认是否合格,对于趋势也无法直观做出判断,而且色差管理所涉及的部门人员众多,信息沟通成本高。
来自两江工厂焊接三车间的设备工程师邓先铭介绍,如今他们通过简道云自主搭建了色差管理系统。通过建立色差监控模块,就可以对颜色标准进行录入。然后通过现场设备设备和简道云仪表盘对车身色差,外饰件色差,及车色差趋势进行监控管理。
此外建立的色差匹配模块和问题管理模块,能够建立车身/外饰件色差超差问题管理台账及车身与外饰件匹配管理台账,同时得益于简道云的流程流转功能,建立了异常车辆返修管理程序,对上述问题能够进行及时的整改及闭环管理。
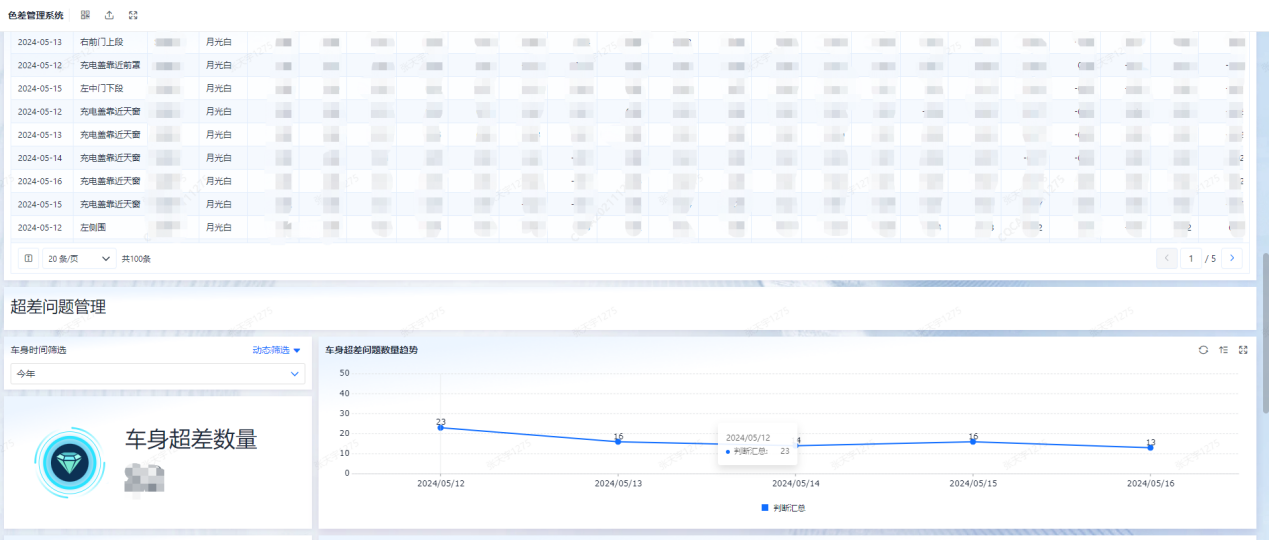
“色差管理应用的使用,帮助我们极大提升了色差管理效率,减少了因色差不合格流向市场导致的顾客抱怨。同时色差管理系统也帮助我们提升了沟通效率,能够清楚对问题车进行管理,防止因沟通失误导致问题流出。”邓先铭说到。
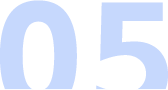
数字人才,未来可期
“51个应用,1216个表单,90%CPS业务的E化替代,日均使用人数1300+,日均操作量8000+,整体办公效率提升50%。”这些具象化的数据背后是两江工厂业务人员在零代码世界不断探索的成功回应,也是他们业务+数字化协同创新的成功实践。
谈及未来,魏泽淇表示,两江工厂将持续探索数字化工具融合发展路线和开展数字化培训,将零代码工具与RPA、Alteryx等数字化工具进行融合,培养多维度全方面人才,为工厂的数字化发展,持续提供人才支持。 |